4.3.9 Ao projetar placas multicamadas, deve-se prestar atenção aos componentes com invólucros metálicos que estão em embalagens plug-in e fazem contato com a placa de circuito impresso. As almofadas da camada superior não devem ser abertas. Eles devem ser cobertos com óleo verde ou tinta serigráfica (como cristais de dois pinos, LEDs de três pinos).
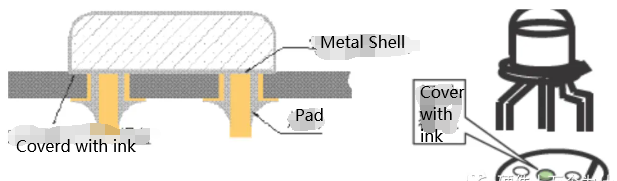
4.3.10 Ao projetar e dispor PCBs, tente minimizar os slots e furos na placa impressa para evitar afetar sua resistência.
4.3.11 Componentes valiosos: Não coloque componentes valiosos nos cantos, bordas, orifícios de montagem, ranhuras, bordas cortantes de painéis ou cantos. Essas posições são áreas de alta tensão da placa impressa, que podem facilmente causar rachaduras e fraturas nas juntas e componentes soldados.
4.3.12 Componentes pesados (como transformadores) não devem ficar longe dos furos de posicionamento para evitar afetar a resistência e deformação da placa impressa. Ao fazer o layout, os componentes mais pesados devem ser colocados embaixo da placa de circuito impresso (também no lado que passa por último na soldagem por onda).
4.3.13 Dispositivos que emitem energia, como transformadores e relés, devem ser mantidos afastados de dispositivos e circuitos suscetíveis a interferências, como amplificadores, microcontroladores, cristais e circuitos de reset, para evitar afetar a confiabilidade durante a operação.
4.3.14 Para CIs em pacotes QFP (que exigem processo de soldagem por onda), eles devem ser colocados em um ângulo de 45 graus e incluir almofadas de solda (conforme mostrado na imagem).
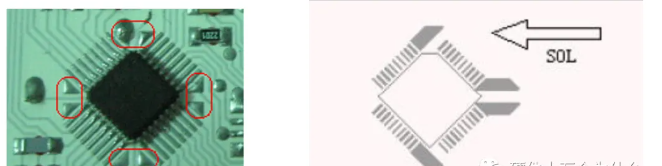
4.3.15 Quando os componentes de montagem em superfície são soldados por onda, nenhum orifício de dissipação de calor deve ser aberto ao redor e abaixo dos componentes com componentes inseridos (como dissipadores de calor, transformadores, etc.) para evitar que a solda da onda 1 (onda perturbadora) aderindo a componentes ou pinos de componentes na placa superior, causando objetos estranhos durante a montagem em processos subsequentes.
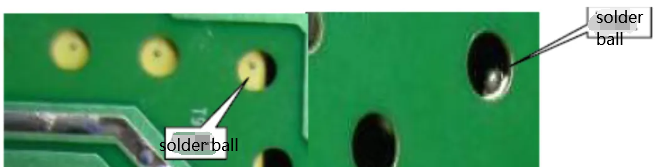
4.3.16 Folhas de cobre de grandes áreas requerem fita isolante para serem conectadas às almofadas.
Para garantir uma boa penetração da solda, as almofadas dos componentes em folhas de cobre de grande área devem ser conectadas às almofadas com fita isolante. Para placas que requerem mais de 5A de corrente, placas isolantes não podem ser usadas. (Ver imagem)

4.3.17 Para evitar desalinhamento e marcação de dispositivos após soldagem por refluxo, a simetria de dissipação de calor das duas extremidades do 0805 e dos componentes de montagem abaixo da superfície deve ser garantida. A largura da conexão entre a almofada e o condutor impresso não deve ultrapassar 0.3mm (para almofadas assimétricas), conforme imagem acima.
4.4 Requisitos de seleção da biblioteca de componentes
4.4.1 A seleção de bibliotecas de pacotes de componentes PCB existentes deve ser confirmada como correta.
A seleção de componentes nas bibliotecas de componentes existentes na PCB deve garantir que o pacote corresponda à forma física, espaçamento entre pinos, diâmetro do furo, etc., do componente.
Para componentes com furo passante, a tolerância entre os pinos do componente e o furo passante deve ser bem combinada (o diâmetro do furo passante é maior que 8–20mil do diâmetro do pino), e a tolerância pode ser aumentada adequadamente para garantir uma boa penetração da solda. Quando nenhum requisito especial é feito, as especificações do furo passante para componentes inseridos manualmente são as seguintes:
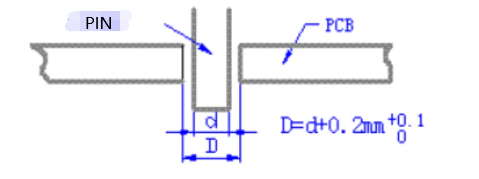
4.4.2 O diâmetro dos componentes deve ser serializado, aumentando 5 mil para acima de 40 mil, ou seja, 40 mil, 45 mil, 50 mil, 55 mil, e diminuindo 4 mil para abaixo de 40 mil, ou seja, 36 mil, 32 mil , 28 mil, 24 mil, 20 mil, 16 mil, 12 mil, 8 mil.
4.4.3 A correspondência entre o diâmetro do pino do dispositivo e o diâmetro do orifício da almofada da PCB e o diâmetro do orifício da almofada de solda do pino do plugue e da soldagem por refluxo corresponde à seguinte:
Diâmetro do pino do dispositivo (D) | Diâmetro do furo da almofada PCB/diâmetro do furo da almofada de solda de refluxo THT) |
D≤1.0 mm | D+0.3mm/+0.15mm |
1.0 mm | D+0.4mm/0.2mm |
D>2.0 mm | D+0.5mm/0.2mm |
Ao estabelecer uma biblioteca de pacotes de componentes, a unidade do diâmetro do furo deve ser convertida em unidades imperiais (mil) e o diâmetro do furo deve atender aos requisitos de serialização.
4.4.4 Projeto de formatos de almofadas:
4.4.4.1 Em princípio, o projeto dos blocos componentes deve atender aos seguintes pontos:
4.4.4.1.1 Tente fazer com que a direção da almofada seja perpendicular à direção do fluxo.
4.4.4.1.2 A largura da almofada é preferencialmente igual ou ligeiramente maior que a largura do componente; o comprimento da almofada é ligeiramente menor que a largura da almofada.
4.4.4.1.3 Aumentar a folga entre as almofadas dos componentes é benéfico para a montagem; pequenas almofadas são recomendadas.
4.4.4.1.4 Não deve haver furos passantes nos ou próximos aos coxins dos componentes MT; caso contrário, durante a soldagem por refluxo, a solda nas almofadas fluirá ao longo dos orifícios, causando soldagem virtual, solda insuficiente e pode até fluir para o outro lado da placa, causando um curto-circuito.
4.4.4.1.5 Os traços nas duas extremidades da almofada devem ser uniformes ou ter capacidade térmica semelhante.
4.4.4.1.6 O tamanho da almofada deve ser simétrico.
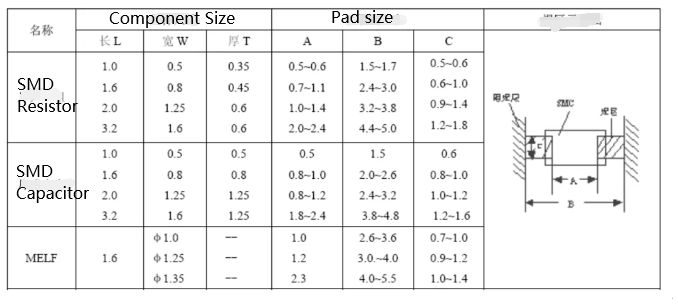
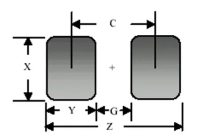
4.4.4.2 Projeto de formatos de almofadas de solda para componentes de chip (veja imagem acima): As dimensões típicas de projeto para almofadas de solda de componentes de chip são mostradas na tabela abaixo. Filmes resistentes à solda correspondentes podem ser projetados fora de cada almofada. O objetivo do filme resistente à solda é evitar a formação de pontes de solda durante a soldagem.
Dimensões do projeto da almofada de solda para componentes passivos – resistores, capacitores, indutores (veja a tabela abaixo, consulte também a imagem e tabela acima)
Parte | Z (mm) | G (mm) | X (mm) | S(ref) | |
Resistores e capacitores de chip | 0201 | 0.76 | 0.24 | 0.30 | 0.26 |
0402 | 1.45 1.5 ~ | 0.35 0.4 ~ | 0.55 | 0.55 | |
C0603 | 2.32 | 0.72 | 0.8 | 1.8 | |
R0603 | 2.4 | 0.6 | 1.0 | 0.9 | |
L0603 | 2.32 | 0.72 | 0.8 | 0.8 | |
C0805 | 2.85 | 0.75 | 1.4 | 1.05 | |
R0805 | 3.1 | 0.9 | 1.6 | 1.1 | |
L0805 | 3.25 | 0.75 | 1.5 | 1.25 | |
1206 | 4.4 | 1.2 | 1.8 | 1.6 | |
1210 | 4.4 | 1.2 | 2.7 | 1.6 | |
1812 | 5.8 | 2.0 | 3.4 | 1.9 | |
1825 | 5.8 | 2.0 | 6.8 | 1.9 | |
2010 | 6.2 | 2.6 | 2.7 | 1.8 | |
2512 | 7.4 | 3.8 | 3.2 | 1.8 | |
3216(Tipo A) | 4.8 | 0.8 | 1.2 | 2.0 | |
Capacitores de tântalo | 3528(Tipo B) | 5.0 | 1.0 | 2.2 | 2.0 |
6032(Tipo C) | 7.6 | 2.4 | 2.2 | 2.6 | |
7343(Tipo D) | 9.0 | 3.8 | 2.4 | 2.6 | |
2012 (0805) | 3.2 | 0.6 | 1.6 | 1.3 | |
3216 (1206) | 4.4 | 1.2 | 2.0 | 1.6 | |
3516 (1406) | 4.8 | 2.0 | 1.8 | 1.4 | |
5923 (2309) | 7.2 | 4.2 | 2.6 | 1.5 | |
Chip 2012(0805) | 3.0 | 1.0 | 1.0 | 1.0 | |
indutores | Chip 3216 (1206) | 4.2 | 1.8 | 1.6 | 1.2 |
Chip 4516 (1806) | 5.8 | 2.6 | 1.0 | 1.6 | |
2825Prec(1110) | 3.8 | 1.0 | 2.4 | 1.4 | |
3225Prec(1210) | 4.6 | 1.0 | 2.0 | 1.8 | |
Dimensões do projeto da almofada de solda de componente passivo:
Componente | Comprimento (mm) | Largura (mm) |
---|---|---|
Resistor | 0.9 – 1.3 | 0.4 – 0.7 |
Capacitor | 0.9 – 1.3 | 0.4 – 0.7 |
Indutor | 0.9 – 1.3 | 0.4 – 0.7 |
Consulte a imagem e a tabela acima para dimensões e configurações específicas do projeto.
4.4.4.3 Projeto da almofada de solda SOP e QFP: Os tamanhos da almofada de solda SOP e QFP podem ser projetados de acordo com IPC-SM-782.
Para os padrões de projeto do SOP, placas de solda QFP (conforme mostrado na tabela abaixo):
O tamanho da almofada de solda deve ser determinado de acordo com o tamanho do componente. A largura da almofada de solda = largura do pino + 2 * altura do pino para melhores efeitos de soldagem. O comprimento da almofada de solda é mostrado na ilustração L2, (L2 = L + b1 + b2; b1 = b2 = 0.3 mm + h; h = altura do pino do componente)
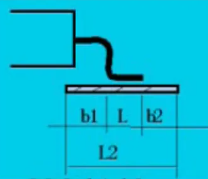
4.4.4.4 Quando nenhum requisito especial for feito, as especificações para placas de solda de componentes montadas através de furos são as seguintes:
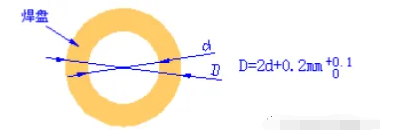
4.4.4.5 Para PINs, capacitores, etc. inseridos manualmente, com espaçamento entre pinos ≤2.0 mm, as especificações para almofadas de solda são: ① Diâmetro da almofada de solda de placa multicamadas = diâmetro do furo + 0.2 ~ 0.4 mm; ② Diâmetro da almofada de solda da placa de camada única = 2×diâmetro do furo
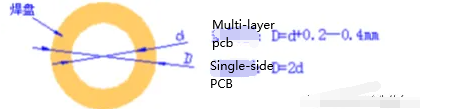
4.4.4.6 Design de almofada de solda IC de montagem em superfície comum, consulte o arquivo anexado (a figura abaixo é apenas uma seleção, consulte o arquivo anexado para dimensões específicas)
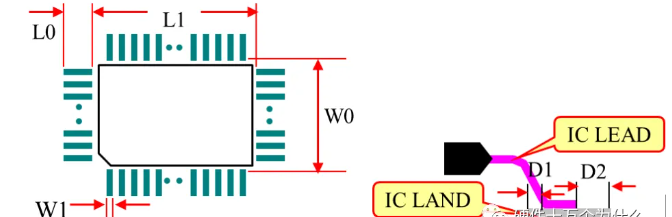
4.4.5 A nova biblioteca de pacotes de componentes de PCB do dispositivo deve ser estabelecida corretamente
4.4.5.1 Dispositivos sem bibliotecas de pacotes de componentes existentes no PCB devem estabelecer novas bibliotecas de pacotes de componentes com base nos dados do dispositivo e garantir que o inventário da serigrafia corresponda aos objetos físicos, especialmente se os componentes eletromagnéticos recém-estabelecidos, componentes estruturais feitos por eles mesmos, etc. , combine a biblioteca de componentes com os dados (carta de confirmação, folha de especificações, desenhos). Novos dispositivos devem estabelecer bibliotecas de componentes que possam atender a diferentes requisitos de processo (soldagem por refluxo, soldagem por onda, soldagem por refluxo através do orifício).
4.4.5.2 Os componentes SMT que requerem soldagem por onda devem usar bibliotecas de placas de solda por onda para montagem em superfície.
4.4.5.3 Os tipos de componentes axiais e pinos de jumper devem ser minimizados para reduzir as ferramentas de moldagem e instalação dos componentes.
4.4.5.4 Diferentes componentes compatíveis com espaçamento de PIN devem ter furos de solda separados, especialmente os pads de solda compatíveis com relés encapsulados devem ser conectados.
4.4.5.5 Os componentes de montagem em superfície não devem ser usados como componentes de depuração para soldagem manual, pois os componentes de montagem em superfície são facilmente danificados por choque térmico durante a soldagem manual.
4.4.5.6 A menos que a verificação experimental seja feita sem problemas, componentes de montagem em superfície com coeficientes de expansão térmica significativamente diferentes da PCB não devem ser selecionados, pois isso pode causar delaminação da almofada de solda.
4.4.5.7 A menos que a verificação experimental seja feita sem problemas, componentes que não sejam de montagem em superfície não devem ser usados como componentes de montagem em superfície. Isto pode exigir soldagem manual, o que resultará em baixa eficiência e confiabilidade.
4.4.5.8 Para PCBs multicamadas, o revestimento de cobre local na lateral como pinos de solda deve garantir que cada camada seja conectada com folha de cobre para aumentar a resistência de adesão do revestimento de cobre. Ao mesmo tempo, a verificação experimental deve ser feita sem problemas. Caso contrário, as placas dupla-face não podem usar o revestimento lateral de cobre como pinos de solda.
4.4.6 Distância de segurança para componentes da tabela de um lado que requerem soldagem por onda para evitar efeito de sombra durante a soldagem por onda, a distância entre os componentes SMT deve atender aos seguintes requisitos:
- Distância entre o mesmo tipo de componentes (conforme mostrado na figura)
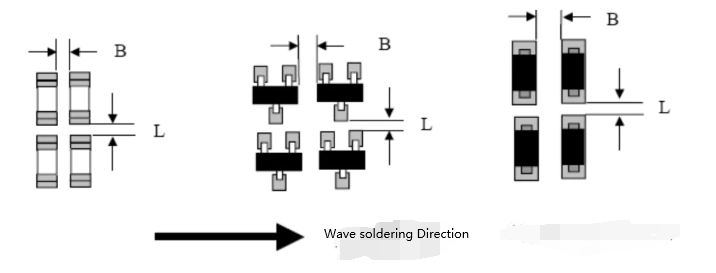
4.6.1 Componentes SMD do mesmo tipo devem ter espaçamento ≥0.3mm, e o espaçamento entre diferentes tipos de componentes deve ser ≥0.13*h+0.3mm (Nota: h refere-se à diferença máxima de altura entre duas peças diferentes) , O espaçamento dos componentes THT deve facilitar a operação e a substituição.
4.6.2 A distância entre o lado externo da almofada de solda do componente de montagem e o lado externo dos componentes de montagem adjacentes deve ser maior que 2 mm.
4.6.3 Componentes SMD devem ser evitados dentro de 3 mm ao redor de componentes frequentemente conectados ou conectores de borda da placa para evitar danos por tensão aos componentes durante a inserção e remoção do conector.
4.6.4 A distância do centro do furo de posicionamento até a borda do componente de montagem em superfície não deve ser inferior a 5.0 mm.
4.6.5 Capacitores cerâmicos maiores que pacotes 0805 devem ser colocados próximos à borda de transmissão ou em áreas com menos tensão, e seus sentidos axiais devem ser paralelos ao sentido de entrada da placa, e capacitores cerâmicos maiores que 1825 devem ser evitados ao máximo. possível. (Comentários reservados)
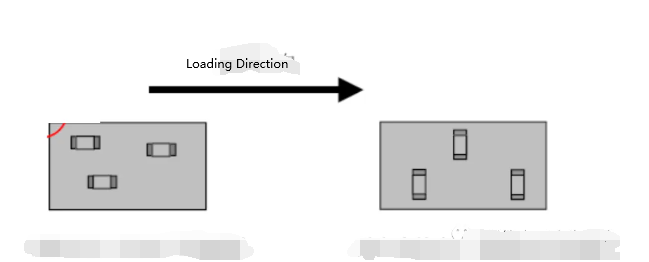
4.4.6.6 SMDs devem ser evitados dentro de 3 mm ao redor de componentes frequentemente conectados ou conectores de borda da placa para evitar danos por tensão aos componentes durante a inserção e remoção do conector. Veja a figura:
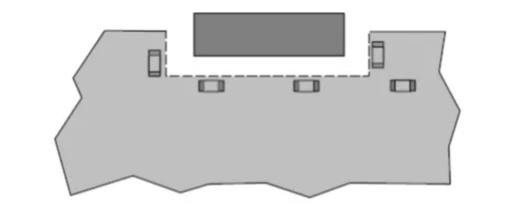
4.4.6.7 Os componentes de montagem em superfície para soldagem por onda devem atender aos requisitos especificados para isolamento. O afastamento dos componentes de montagem em superfície para soldagem por onda deve ser inferior a 0.15 mm. Caso contrário, eles não devem ser colocados no lado B para soldagem por onda. Se o afastamento do componente estiver entre 0.15 mm e 0.2 mm, uma folha de cobre pode ser colocada sob o corpo do componente para reduzir a distância entre a parte inferior do componente e a superfície da PCB.
4.4.6.8 A distância mínima de segurança para pontos de solda através do orifício durante a soldagem por onda foi determinada para garantir que os pontos de solda não se conectem durante a soldagem por onda. A distância entre as bordas dos pontos de teste traseiro deve ser maior que 1.0 mm.
4.4.6.9 O espaçamento entre as placas de solda de componentes através de furos que requerem soldagem por onda deve ser maior que 1.0 mm para garantir que os pontos de solda não formem ponte durante a soldagem por onda (incluindo o espaçamento entre as bordas das placas de solda dos pinos dos componentes). O passo preferido para pinos componentes de furo passante (passo) é ≧2.0 mm
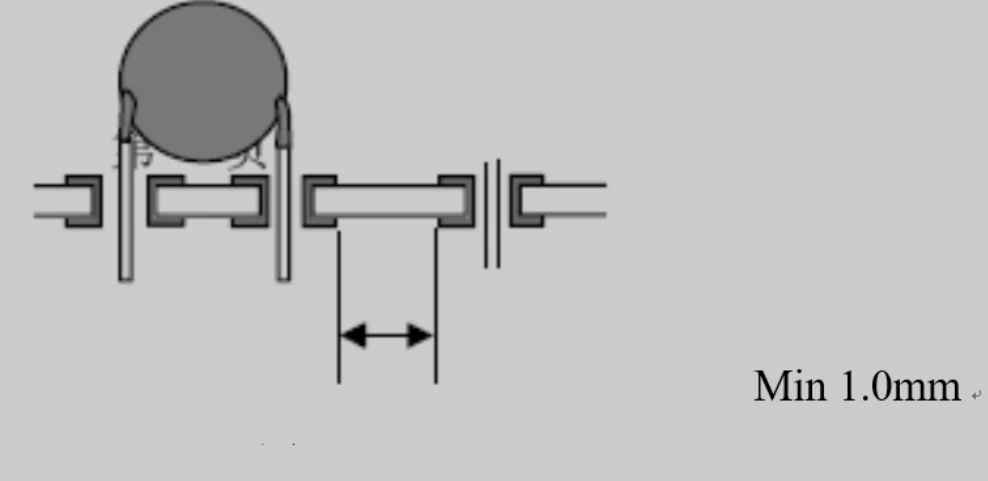
4.4.6.10 Quando há muitos pinos por linha em componentes plug-in, e os componentes são dispostos com placas de solda paralelas à direção de inserção da PCB, uma abordagem recomendada para espaçamento de borda da placa de solda adjacente entre 0.6-1.0 mm é usar oval em forma de almofadas de solda ou para adicionar almofadas de estanhagem.
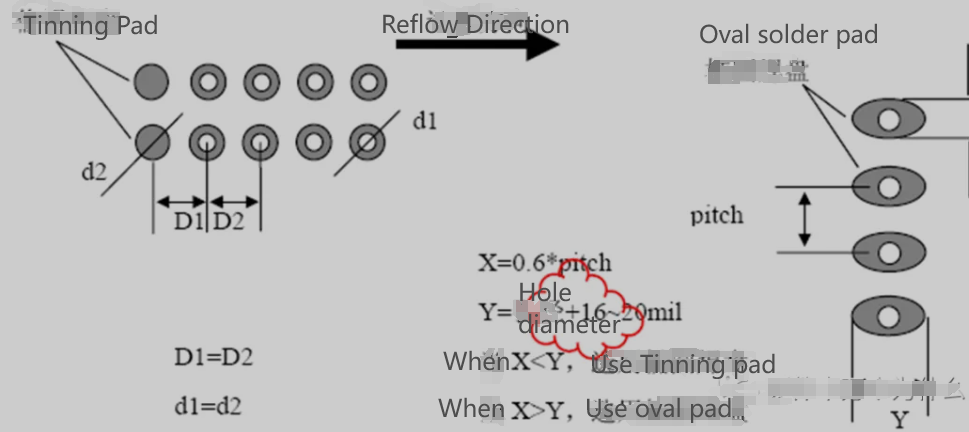
4.4.6.11 O espaçamento mínimo entre os componentes de montagem saliente deve atender aos seguintes requisitos:
Para posicionamento da máquina:
- Entre componentes do mesmo tipo: ≥ 0.3 mm
- Entre componentes de tipos diferentes: ≥ 0.13 * h + 0.3 mm (onde h é a diferença máxima de altura entre componentes vizinhos)
Para posicionamento manual:
- Entre componentes: ≥ 1.5mm.
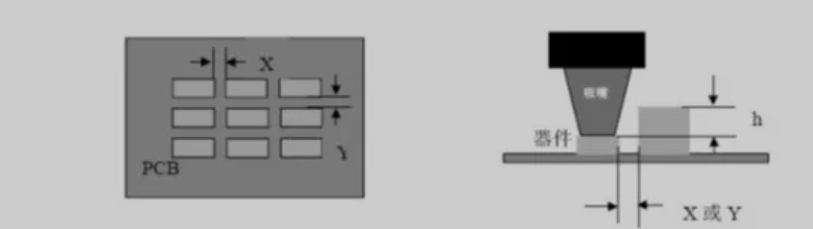
4.4.6.12 A distância da borda externa dos componentes até as bordas dos trilhos da placa deve ser maior ou igual a 5mm. Isto é para garantir que as garras da pista transportadora não toquem nos componentes durante a soldagem por onda ou por refluxo. Caso este requisito não seja atendido, a PCB deverá ser processada com tratamento de borda, e a distância entre os componentes e o V-CUT deverá ser ≥ 1mm.
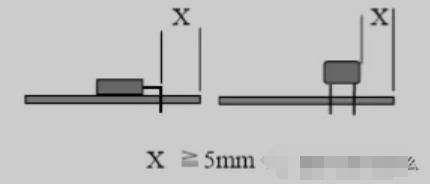
4.4.6.13 Deve ser reservado espaço adequado em torno dos componentes ajustáveis e conectáveis para depuração e manutenção. A orientação dos componentes ajustáveis e o espaço reservado para componentes conectáveis devem ser determinados com base no layout de instalação do PCBA e no método de depuração dos componentes ajustáveis.
4.4.6.14 Todos os componentes magnéticos plug-in devem ter base robusta, sendo proibida a utilização de indutores plug-in sem base.
4.4.6.15 Evite projetar os pinos dos transformadores polarizados de forma simétrica. Quando um pino não estiver conectado a um circuito, certifique-se de adicionar uma almofada de solda para aumentar a resistência da solda.
4.4.6.16 Nenhum componente ou vestígio deve ser colocado na área proibida do furo de montagem (excluindo os vestígios e a folha de cobre do próprio furo de montagem).
4.4.6.17 A distância entre os componentes metálicos da carcaça e os demais componentes deve atender às normas de segurança. A disposição dos componentes do invólucro metálico deve garantir que a distância de outros componentes atenda aos regulamentos de segurança.
4.4.6.18 Requisitos para layout de componentes usando soldagem por refluxo passante: a. Para PCBs com tamanho de borda sem transporte superior a 300 mm, componentes pesados devem ser evitados no meio da PCB para reduzir o impacto do peso dos componentes inseridos na deformação da PCB durante a soldagem, bem como o impacto da inserção de componentes nos componentes já colocado no tabuleiro. b. Para facilitar a inserção, os componentes devem ser colocados próximos à lateral da operação de inserção. c. Para componentes mais longos (como soquetes de cartão de memória), a direção do comprimento deve ser consistente com a direção do transporte. Quando vários pinos de um componente estão na mesma linha reta, os conectores, os componentes do pacote DIP e os componentes do pacote T220 devem ser organizados de modo que seus eixos fiquem paralelos à direção da soldagem por onda. Componentes mais leves, como diodos e resistores de 1/4W, devem ser dispostos de modo que seus eixos fiquem perpendiculares à direção da onda de soldagem. Isso evita a flutuação durante a soldagem por onda devido à solidificação de uma extremidade antes da outra e evita o uso de placas de solda quadradas para componentes de furo passante (o que pode levar a uma soldagem e ponte inadequadas).