4.3.9 Quando si progettano schede multistrato, è necessario prestare attenzione ai componenti con involucri metallici che si trovano in pacchetti plug-in e entrano in contatto con il circuito stampato. Le protezioni dello strato superiore non devono essere aperte. Devono essere ricoperti con olio verde o inchiostro serigrafico (come cristalli a due pin, LED a tre pin).
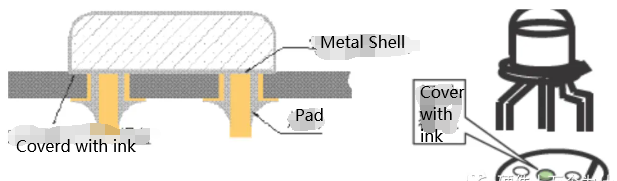
4.3.10 Durante la progettazione e la disposizione dei PCB, cercare di ridurre al minimo le fessure e i fori nel circuito stampato per evitare di comprometterne la resistenza.
4.3.11 Componenti di valore: non posizionare componenti di valore sugli angoli, sui bordi, sui fori di montaggio, sulle fessure, sui bordi taglienti dei pannelli elettrici o sugli angoli. Queste posizioni sono aree ad alto stress della scheda stampata, che possono facilmente causare crepe e fratture nei giunti e nei componenti di saldatura.
4.3.12 I componenti pesanti (come i trasformatori) non dovrebbero essere lontani dai fori di posizionamento per evitare di compromettere la resistenza e la deformazione del circuito stampato. Durante la disposizione, i componenti più pesanti devono essere posizionati sotto il PCB (anche il lato che passa per ultimo attraverso la saldatura ad onda).
4.3.13 I dispositivi che emettono energia, come trasformatori e relè, dovrebbero essere tenuti lontani da dispositivi e circuiti suscettibili alle interferenze, come amplificatori, microcontrollori, cristalli e circuiti di ripristino, per evitare di comprometterne l'affidabilità durante il funzionamento.
4.3.14 Per i circuiti integrati nei pacchetti QFP (che richiedono un processo di saldatura a onda), devono essere posizionati con un angolo di 45 gradi e includere piazzole di saldatura (come mostrato nell'immagine).
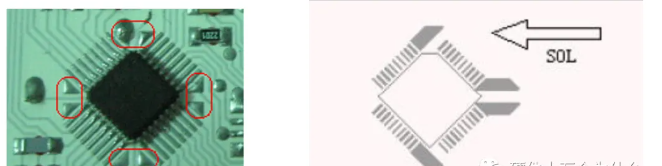
4.3.15 Quando i componenti a montaggio superficiale sono saldati ad onda, non devono essere aperti fori di dissipazione del calore intorno e sotto i componenti con componenti inseriti (come dissipatori di calore, trasformatori, ecc.) per evitare che la saldatura dell'onda 1 (onda di disturbo) attaccarsi ai componenti o ai perni dei componenti sulla scheda superiore, causando corpi estranei durante l'assemblaggio nei processi successivi.
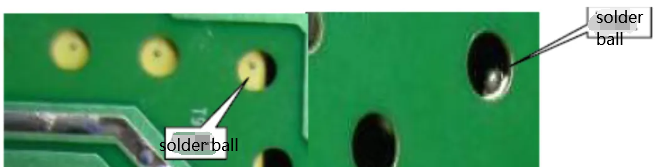
4.3.16 Le lamine di rame di ampia area richiedono il collegamento del nastro isolante ai cuscinetti.
Per garantire una buona penetrazione della saldatura, le piazzole dei componenti su lamine di rame di grandi dimensioni devono essere collegate alle piazzole con nastro isolante. Per i cuscinetti che richiedono più di 5 A di corrente, non è possibile utilizzare cuscinetti isolanti. (Vedi immagine)

4.3.17 Per evitare il disallineamento e la rimozione definitiva dei dispositivi dopo la saldatura a rifusione, dovrebbe essere garantita la simmetria di dissipazione del calore delle due estremità di 0805 e dei componenti a montaggio superficiale inferiori. La larghezza della connessione tra il pad e il conduttore stampato non deve superare 0.3 mm (per pad asimmetrici), come mostrato nell'immagine sopra.
4.4 Requisiti per la selezione della libreria dei componenti
4.4.1 La selezione delle librerie dei pacchetti di componenti PCB esistenti dovrebbe essere confermata come corretta.
La selezione dei componenti nelle librerie di componenti esistenti sul PCB dovrebbe garantire che il pacchetto corrisponda alla forma fisica, alla spaziatura dei pin, al diametro del foro, ecc. del componente.
Per i componenti a foro passante, la tolleranza tra i perni del componente e il foro passante deve essere ben abbinata (il diametro del foro passante è maggiore di 8-20 mil del diametro del perno) e la tolleranza può essere opportunamente aumentata per garantire una buona penetrazione della saldatura. Quando non vengono stabiliti requisiti speciali, le specifiche del foro passante per i componenti inseriti manualmente sono le seguenti:
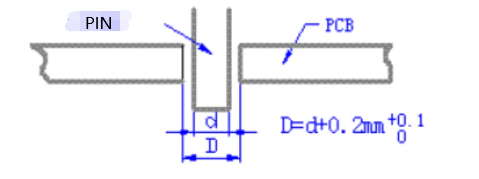
4.4.2 Il diametro dei componenti deve essere serializzato, aumentando di 5 mil per oltre 40 mil, ovvero 40 mil, 45 mil, 50 mil, 55 mil e diminuendo di 4 mil per inferiori a 40 mil, ovvero 36 mil, 32 mil , 28 milioni, 24 milioni, 20 milioni, 16 milioni, 12 milioni, 8 milioni.
4.4.3 La corrispondenza tra il diametro del pin del dispositivo e il diametro del foro del pad del PCB, e il diametro del foro del pad di saldatura del pin della spina e la saldatura a rifusione corrisponde come segue:
Diametro perno del dispositivo (D) | Diametro foro piastra PCB/Diametro foro piastra saldatura a rifusione THT) |
D≤1.0 mm | D+0.3 mm/+0.15 mm |
1.0 mm | D+0.4 mm/0.2 mm |
D>2.0 mm | D+0.5 mm/0.2 mm |
Quando si stabilisce una libreria di pacchetti di componenti, l'unità del diametro del foro deve essere convertita in unità imperiali (mil) e il diametro del foro deve soddisfare i requisiti di serializzazione.
4.4.4 Progettazione delle forme dei pad:
4.4.4.1 In linea di principio, la progettazione dei componenti dei cuscinetti dovrebbe rispettare i seguenti punti:
4.4.4.1.1 Cercare di rendere la direzione del tampone perpendicolare alla direzione del flusso.
4.4.4.1.2 La larghezza del tampone è preferibilmente uguale o leggermente maggiore della larghezza del componente; la lunghezza del pad è leggermente inferiore alla larghezza del pad.
4.4.4.1.3 Aumentare lo spazio tra i cuscinetti dei componenti è vantaggioso per l'assemblaggio; si consigliano cuscinetti piccoli.
4.4.4.1.4 Non dovrebbero esserci fori passanti sopra o vicino ai cuscinetti dei componenti MT; altrimenti, durante la saldatura a riflusso, la saldatura sui pad scorrerà lungo i fori passanti, causando una saldatura virtuale, una saldatura insufficiente e potrebbe persino fluire verso l'altro lato della scheda provocando un cortocircuito.
4.4.4.1.5 Le tracce su entrambe le estremità del tampone dovrebbero essere uniformi o avere una capacità termica simile.
4.4.4.1.6 La dimensione del pad deve essere simmetrica.
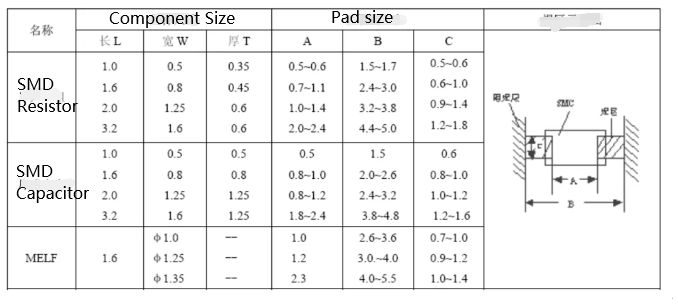
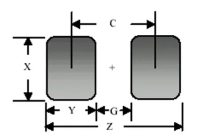
4.4.4.2 Progettazione delle forme delle piazzole di saldatura per componenti di chip (vedere l'immagine sopra): Le dimensioni di progettazione tipiche per le piazzole di saldatura di componenti di chip sono mostrate nella tabella seguente. È possibile progettare pellicole resistenti alla saldatura corrispondenti all'esterno di ciascun pad. Lo scopo della pellicola di saldatura è quello di prevenire i ponti di saldatura durante la saldatura.
Dimensioni del design delle piastre di saldatura per componenti passivi: resistori, condensatori, induttori (vedere la tabella seguente, fare riferimento anche all'immagine e alla tabella sopra)
Parte | Z (millimetro) | G (millimetro) | X (millimetro) | Y(rif) | |
Resistori e condensatori a chip | 0201 | 0.76 | 0.24 | 0.30 | 0.26 |
0402 | 1.45 ~ 1.5 | 0.35 ~ 0.4 | 0.55 | 0.55 | |
C0603 | 2.32 | 0.72 | 0.8 | 1.8 | |
R0603 | 2.4 | 0.6 | 1.0 | 0.9 | |
L0603 | 2.32 | 0.72 | 0.8 | 0.8 | |
C0805 | 2.85 | 0.75 | 1.4 | 1.05 | |
R0805 | 3.1 | 0.9 | 1.6 | 1.1 | |
L0805 | 3.25 | 0.75 | 1.5 | 1.25 | |
1206 | 4.4 | 1.2 | 1.8 | 1.6 | |
1210 | 4.4 | 1.2 | 2.7 | 1.6 | |
1812 | 5.8 | 2.0 | 3.4 | 1.9 | |
1825 | 5.8 | 2.0 | 6.8 | 1.9 | |
2010 | 6.2 | 2.6 | 2.7 | 1.8 | |
2512 | 7.4 | 3.8 | 3.2 | 1.8 | |
3216(Tipo A) | 4.8 | 0.8 | 1.2 | 2.0 | |
Condensatori al tantalio | 3528(Tipo B) | 5.0 | 1.0 | 2.2 | 2.0 |
6032(Tipo C) | 7.6 | 2.4 | 2.2 | 2.6 | |
7343(Tipo D) | 9.0 | 3.8 | 2.4 | 2.6 | |
2012 (0805) | 3.2 | 0.6 | 1.6 | 1.3 | |
3216 (1206) | 4.4 | 1.2 | 2.0 | 1.6 | |
3516 (1406) | 4.8 | 2.0 | 1.8 | 1.4 | |
5923 (2309) | 7.2 | 4.2 | 2.6 | 1.5 | |
2012Chip(0805) | 3.0 | 1.0 | 1.0 | 1.0 | |
induttori | 3216 Chip(1206) | 4.2 | 1.8 | 1.6 | 1.2 |
4516 Chip(1806) | 5.8 | 2.6 | 1.0 | 1.6 | |
2825Prec(1110) | 3.8 | 1.0 | 2.4 | 1.4 | |
3225Prec(1210) | 4.6 | 1.0 | 2.0 | 1.8 | |
Dimensioni del design del cuscinetto di saldatura del componente passivo:
Componente | Lunghezza (mm) | Larghezza (mm) |
---|---|---|
Resistore | 0.9 - 1.3 | 0.4 - 0.7 |
Condensatore | 0.9 - 1.3 | 0.4 - 0.7 |
Induttore | 0.9 - 1.3 | 0.4 - 0.7 |
Fare riferimento all'immagine e alla tabella sopra per dimensioni e configurazioni di progettazione specifiche.
4.4.4.3 Design delle piazzole di saldatura SOP e QFP: le dimensioni delle piazzole di saldatura SOP e QFP possono essere progettate secondo IPC-SM-782.
Per gli standard di progettazione di SOP, piazzole di saldatura QFP (come mostrato nella tabella seguente):
La dimensione del pad di saldatura deve essere determinata in base alla dimensione del componente. La larghezza del pad di saldatura = larghezza del perno + 2 * altezza del perno per i migliori effetti di saldatura. La lunghezza del pad di saldatura è mostrata nell'illustrazione L2, (L2 = L + b1 + b2; b1 = b2 = 0.3 mm + h; h = altezza pin del componente)
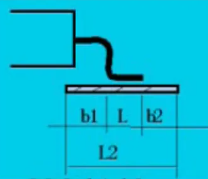
4.4.4.4 Quando non vengono stabiliti requisiti speciali, le specifiche per i pad di saldatura dei componenti montati su foro passante sono le seguenti:
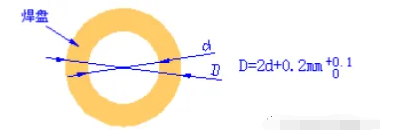
4.4.4.5 Per PIN, condensatori, ecc. inseriti manualmente, con spaziatura tra i pin ≤2.0 mm, le specifiche per i pad di saldatura sono: ① Diametro del pad di saldatura della scheda multistrato = diametro del foro + 0.2~0.4 mm; ② Diametro del pad di saldatura della scheda a strato singolo = 2×diametro del foro
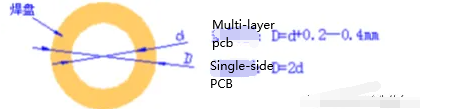
4.4.4.6 Design comune delle piastre di saldatura CI a montaggio superficiale, vedere il file allegato (la figura seguente è solo una selezione, vedere il file allegato per dimensioni specifiche)
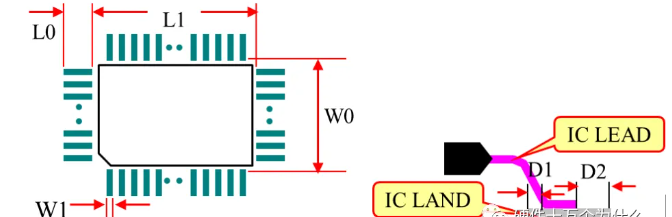
4.4.5 La nuova libreria di pacchetti di componenti PCB del dispositivo deve essere stabilita correttamente
4.4.5.1 I dispositivi senza librerie di pacchetti di componenti esistenti sul PCB dovrebbero stabilire nuove librerie di pacchetti di componenti basate sui dati del dispositivo e garantire che l'inventario serigrafico corrisponda agli oggetti fisici, in particolare se si tratta di componenti elettromagnetici di nuova creazione, componenti strutturali autoprodotti, ecc. , abbinare la libreria dei componenti ai dati (lettera di conferma, scheda tecnica, disegni). I nuovi dispositivi dovrebbero creare librerie di componenti in grado di soddisfare diversi requisiti di processo (saldatura a rifusione, saldatura ad onda, saldatura a rifusione a foro passante).
4.4.5.2 I componenti SMT che richiedono la saldatura a onda dovrebbero utilizzare librerie di piastre di saldatura a onda a montaggio superficiale.
4.4.5.3 I tipi di componenti assiali e i pin dei ponticelli dovrebbero essere ridotti al minimo per ridurre gli strumenti di stampaggio e installazione dei componenti.
4.4.5.4 I diversi componenti compatibili con spaziatura PIN dovrebbero avere fori di saldatura separati, in particolare i pad di saldatura compatibili con relè incapsulati dovrebbero essere collegati.
4.4.5.5 I componenti a montaggio superficiale non devono essere utilizzati come componenti di debug per la saldatura manuale, poiché i componenti a montaggio superficiale vengono facilmente danneggiati dallo shock termico durante la saldatura manuale.
4.4.5.6 A meno che la verifica sperimentale non venga eseguita senza problemi, non dovrebbero essere selezionati componenti a montaggio superficiale con coefficienti di dilatazione termica significativamente diversi dal PCB, poiché ciò potrebbe causare la delaminazione delle piazzole di saldatura.
4.4.5.7 A meno che la verifica sperimentale non venga eseguita senza problemi, i componenti non a montaggio superficiale non dovrebbero essere utilizzati come componenti a montaggio superficiale. Ciò potrebbe richiedere la saldatura manuale, che si tradurrà in una bassa efficienza e affidabilità.
4.4.5.8 Per i PCB multistrato, la placcatura in rame locale sul lato come pin di saldatura deve garantire che ogni strato sia collegato con un foglio di rame per aumentare la forza di adesione della placcatura in rame. Allo stesso tempo, la verifica sperimentale deve essere eseguita senza problemi. Altrimenti, le schede a doppia faccia non possono utilizzare la placcatura in rame laterale come perni di saldatura.
4.4.6 Distanza di sicurezza per i componenti del tabellone su un solo lato che richiedono la saldatura a onda per evitare l'effetto ombra durante la saldatura a onda, la distanza tra i componenti SMT deve soddisfare i seguenti requisiti:
- Distanza tra componenti della stessa tipologia (come mostrato in figura)
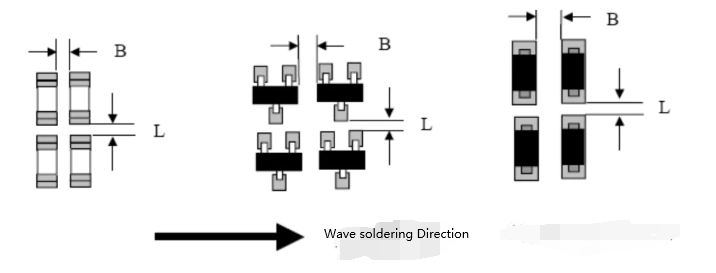
4.6.1 I componenti SMD dello stesso tipo devono avere una spaziatura di ≥ 0.3 mm e la spaziatura tra diversi tipi di componenti deve essere ≥ 0.13*h+0.3 mm (Nota: h si riferisce alla differenza di altezza massima tra due parti diverse) , la spaziatura dei componenti THT dovrebbe facilitare il funzionamento e la sostituzione.
4.6.2 La distanza tra il lato esterno del pad di saldatura del componente di montaggio e il lato esterno dei componenti di montaggio adiacenti deve essere maggiore di 2 mm.
4.6.3 I componenti SMD dovrebbero essere evitati entro 3 mm attorno ai componenti frequentemente collegati o ai connettori sul bordo della scheda per evitare danni da stress ai componenti durante l'inserimento e la rimozione del connettore.
4.6.4 La distanza dal centro del foro di posizionamento al bordo del componente di montaggio superficiale non deve essere inferiore a 5.0 mm.
4.6.5 I condensatori ceramici più grandi di 0805 dovrebbero essere posizionati vicino al bordo di trasmissione o in aree con meno stress, e le loro direzioni assiali dovrebbero essere parallele alla direzione di ingresso della scheda, e i condensatori ceramici più grandi di 1825 dovrebbero essere evitati quanto più possibile. (Commenti riservati)
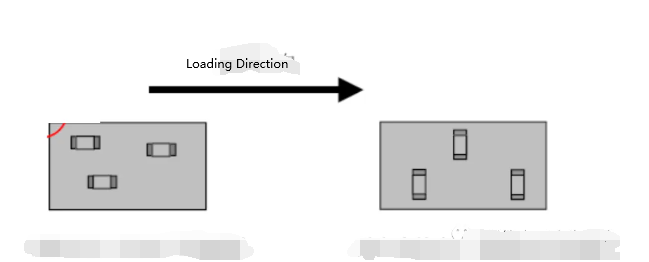
4.4.6.6 Gli SMD dovrebbero essere evitati entro 3 mm attorno ai componenti frequentemente collegati o ai connettori sul bordo della scheda per evitare danni da stress ai componenti durante l'inserimento e la rimozione del connettore. Guarda la figura:
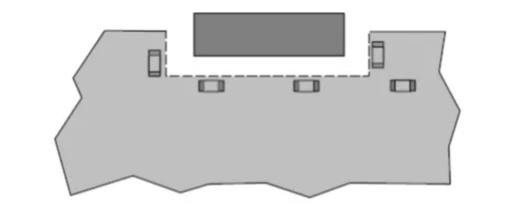
4.4.6.7 I componenti a montaggio superficiale per la saldatura ad onda devono soddisfare i requisiti specificati per lo stand-off. Lo stand-off dei componenti a montaggio superficiale per la saldatura a onda deve essere inferiore a 0.15 mm. Altrimenti non dovrebbero essere posizionati sul lato B per la saldatura ad onda. Se la distanza del componente è compresa tra 0.15 mm e 0.2 mm, è possibile posizionare un foglio di rame sotto il corpo del componente per ridurre la distanza tra la parte inferiore del componente e la superficie del PCB.
4.4.6.8 La distanza minima di sicurezza per i punti di saldatura a foro passante durante la saldatura ad onda è stata determinata per garantire che i punti di saldatura non si sovrappongano durante la saldatura ad onda, la distanza tra i bordi dei punti di prova posteriori deve essere maggiore di 1.0 mm.
4.4.6.9 La spaziatura tra le piazzole di saldatura dei componenti a foro passante che richiedono la saldatura a onda deve essere maggiore di 1.0 mm per garantire che i punti di saldatura non si sovrappongano durante la saldatura a onda (inclusa la spaziatura tra i bordi delle piazzole di saldatura dei pin dei componenti). Il passo preferito per i perni dei componenti con foro passante (passo) è ≧2.0 mm
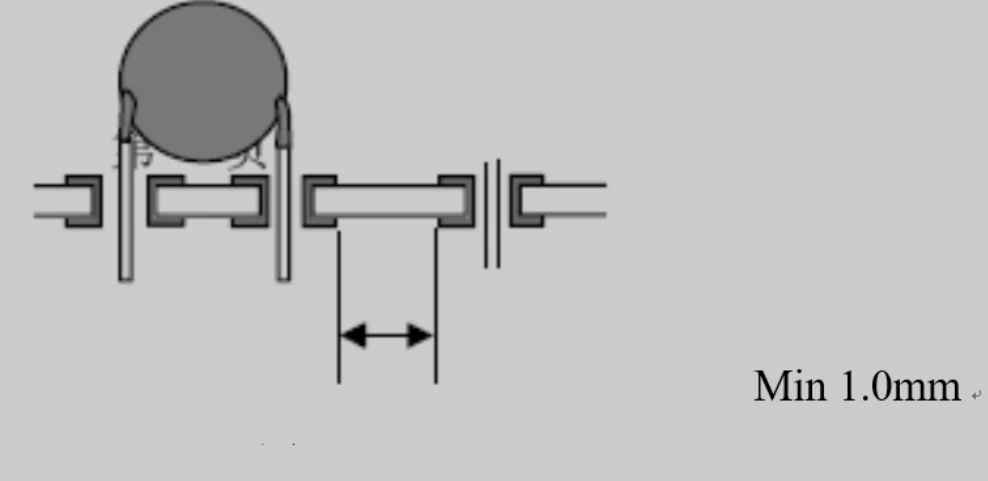
4.4.6.10 Quando ci sono molti pin per fila sui componenti plug-in e i componenti sono disposti con piazzole di saldatura parallele alla direzione di inserimento del PCB, un approccio consigliato per una spaziatura dei bordi delle piazzole di saldatura adiacenti compresa tra 0.6 e 1.0 mm consiste nell'utilizzare una forma ovale cuscinetti di saldatura a forma di o per aggiungere cuscinetti di stagnatura.
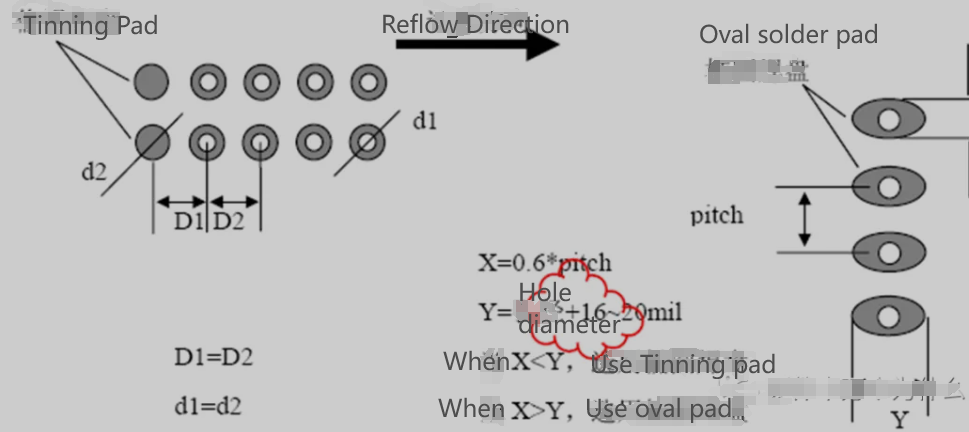
4.4.6.11 La spaziatura minima tra i componenti a montaggio superficiale deve soddisfare i seguenti requisiti:
Per il posizionamento della macchina:
- Tra componenti dello stesso tipo: ≥ 0.3 mm
- Tra componenti di diversa tipologia: ≥ 0.13 * h + 0.3mm (dove h è la massima differenza di altezza tra componenti vicini)
Per il posizionamento manuale:
- Tra i componenti: ≥ 1.5 mm.
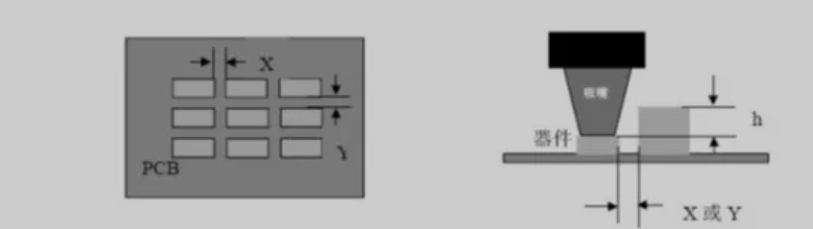
4.4.6.12 La distanza dal bordo esterno dei componenti ai bordi delle piste del pannello deve essere maggiore o uguale a 5 mm. Questo per garantire che gli artigli del binario di trasporto non tocchino i componenti durante la saldatura ad onda o la saldatura a rifusione. Se questo requisito non viene soddisfatto, il PCB deve essere lavorato con un trattamento dei bordi e la distanza tra i componenti e il V-CUT deve essere ≥ 1 mm.
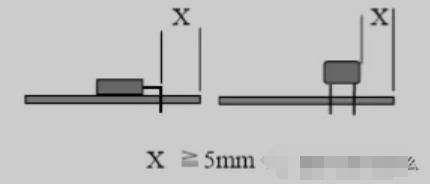
4.4.6.13 Uno spazio adeguato dovrebbe essere riservato attorno ai componenti regolabili e collegabili per il debug e la manutenzione. L'orientamento dei componenti regolabili e lo spazio riservato ai componenti collegabili devono essere determinati in base al layout di installazione PCBA e al metodo di debug dei componenti regolabili.
4.4.6.14 Tutti i componenti magnetici plug-in devono avere una base robusta ed è vietato l'uso di induttori plug-in senza base.
4.4.6.15 Evitare di progettare simmetricamente i pin dei trasformatori polarizzati. Quando un pin non è collegato a un circuito, assicurarsi di aggiungere un pad di saldatura per aumentare la resistenza della saldatura.
4.4.6.16 Nessun componente o traccia deve essere posizionato nell'area vietata del foro di montaggio (escluse le tracce e la lamina di rame del foro di montaggio stesso).
4.4.6.17 La distanza tra i componenti metallici dell'involucro e gli altri componenti deve soddisfare le norme di sicurezza. La disposizione dei componenti dell'involucro metallico dovrebbe garantire che la distanza dagli altri componenti soddisfi le norme di sicurezza.
4.4.6.18 Requisiti per la disposizione dei componenti che utilizzano la saldatura a rifusione a foro passante: a. Per i PCB con dimensioni del bordo non convogliato superiori a 300 mm, è necessario evitare componenti pesanti al centro del PCB per ridurre l'impatto del peso dei componenti inseriti sulla deformazione del PCB durante la saldatura, nonché l'impatto dell'inserimento di componenti sui componenti. già piazzato sul tabellone. B. Per facilitare l'inserimento, i componenti devono essere posizionati vicino al lato dell'operazione di inserimento. C. Per componenti più lunghi (come gli zoccoli per schede di memoria), la direzione della lunghezza deve essere coerente con la direzione di trasporto. Quando più pin di un componente si trovano sulla stessa linea retta, i connettori, i componenti del pacchetto DIP e i componenti del pacchetto T220 devono essere disposti in modo che i loro assi siano paralleli alla direzione della saldatura a onda. I componenti più leggeri come diodi e resistori da 1/4 W dovrebbero essere disposti in modo che i loro assi siano perpendicolari alla direzione dell'onda di saldatura. Ciò impedisce il galleggiamento durante la saldatura a onda dovuta alla solidificazione di un'estremità prima dell'altra ed evita l'uso di cuscinetti di saldatura quadrati per componenti a foro passante (che possono portare a saldature e ponti inadeguati).