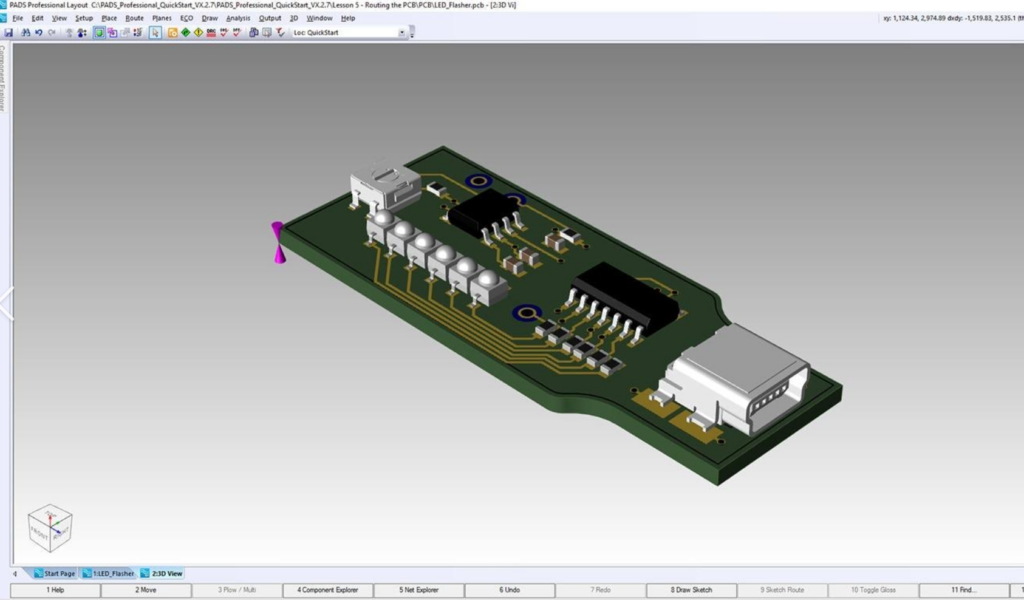
- 目的
PCB パッド設計プロセスを標準化し、PCB パッド設計プロセスの関連パラメータを定義して、PCB 設計が製造性、テスト容易性、安全規制、EMC、EMI などの技術仕様要件を確実に満たすようにし、プロセス、技術、品質の利点を構築します。 、製品設計のコスト。
- 対象領域
この仕様は家庭用電子製品の PCB プロセス設計に適用され、PCB 設計、PCB バッチ生産プロセスのレビュー、および単一基板プロセスのレビューを含むがこれらに限定されない活動に適用されます。
本仕様書の内容と以前の関連規格または仕様書の内容との間に矛盾がある場合には、本仕様書が優先するものとします。
- 参考文献
TS—S0902010001 「情報技術機器 PCB 安全設計仕様書」
TS—SOE0199001「電子機器の強制空冷設計仕様書」
TS—SOE0199002「電子機器の自然冷却熱設計仕様」
IEC60194「プリント基板の設計、製造、および組立 - 用語と定義」
IPC—A—600F 「プリント基板の適合性」
IEC60950
- 仕様内容
4.1 パッドの定義 スルーホールパッドの外形は、通常、円形、正方形、楕円形となります。具体的なサイズの定義については以下で詳しく説明します。名詞の定義は図に示すとおりです。
- 穴のサイズ:
物理的なピンが円形の場合: 穴のサイズ (直径) = 実際のピンの直径 + 0.20∽0.30mm (8.0∽12.0MIL) がおよそです。
物理ピンが正方形または長方形の場合: 穴サイズ (直径) = 実際のピンの対角サイズ + 0.10∽0.20mm (4.0∽8.0MIL) がおよそです。
- パッドサイズ:
標準パッドサイズ=穴サイズ(直径)+約0.50mm(20.0MIL)となります。
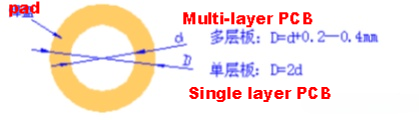
4.2 パッド関連仕様 4.2.1 すべての片面パッドの最小サイズは 0.25mm 以上であり、パッド全体の最大直径はコンポーネントの穴の直径の 1.8 倍を超えません。一般に、スルーホール コンポーネントでは円形のパッドが使用され、パッドの直径は穴の直径の少なくとも 2 倍になります。片面基板パッドの直径は 2.5mm 以上です。両面基板のパッド サイズと穴径の最適な比率は 0.5 で、自動挿入機に適したコンポーネントの場合、両面基板のパッドは標準の穴径 + 0.6 ~ +XNUMX mm です。
4.2.2 0.4 つのパッドの端の間の距離は 0.5 mm より大きいことが望ましく、はんだ波の方向に垂直なパッドの列の場合、1.6 つのパッドの端の間の距離は 0.3 mm より大きい必要があります (この時点では)。 、このパッドの列はワイヤ グループまたはソケットとみなすことができ、それらの間の距離が近すぎるとブリッジングが発生しやすくなります)。密配線の場合は、楕円形の細長い接続パッドを使用することをお勧めします。片面基板パッドの直径または最小幅は 0.2 mm、または片面基板の片面パッドの場合は少なくとも 1.4、両面基板の場合は最小 XNUMX mm を確保します。パッドが大きすぎると、不必要なブリッジングが発生する可能性があります。密に配線する場合は、円形で細長いパッドを使用することをお勧めします。パッドの直径は通常 XNUMX mm、またはそれより小さいです。
4.2.3 穴の直径が 1.2mm を超えるパッド、またはパッドの直径が 3.0mm を超えるパッドは、星型または花型のパッドとして設計する必要があります。プラグイン部品の場合は、はんだ付け時の銅箔の破損を避けるために、片面基板の端の接続を銅箔で完全に覆う必要があります。両面基板の最低要件はドリップメッキである必要があります(環状穴制御セクションの詳細については、添付の付録を参照してください)。図に示すように:
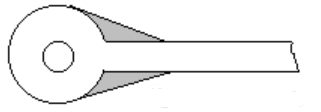
4.2.4 ソケット コネクタや重量のあるデバイスなどのすべての耐力デバイスでは、パッド リードの 2 mm 以内を覆う銅箔の幅を可能な限り大きくする必要があり、空のパッドが存在しないように設計する必要があります。パッドに十分な錫の消耗があり、ソケットに外力が加わっても銅箔が剥がれにくいことを確認してください。大型部品(トランス、直径15.0mm以上の電解コンデンサ、大電流のソケットなど)の場合、上側の銅箔および錫めっきの拡大面積は以下のとおりとなります。斜線部分の最小面積はパッド面積と等しくなければなりません。または花形または星形のパッドとして設計されています。
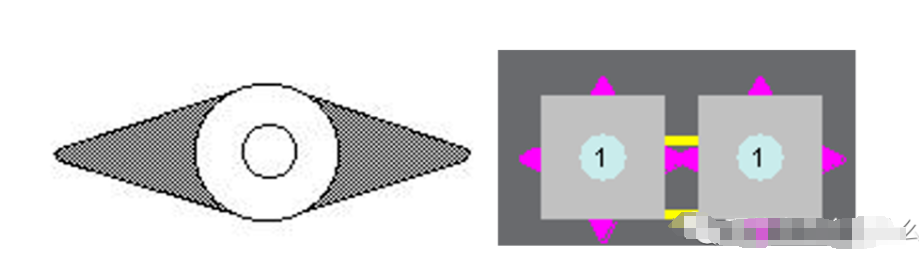
4.2.5 機械で挿入されるすべての部品は、曲げられた足のはんだ接合部が確実に満たされるように、曲げられた足の方向に沿ったドリップパッドとして設計される必要があります。水平成分の場合は左右の足を直接内側に曲げ、垂直成分の場合は左足を下に15°、右足を上に15°曲げます。それらと周囲のパッドの間のエッジ間隔が少なくとも 0.4 より大きいことを確認するように注意してください。

4.2.6 プリント基板上に大面積のグランドおよび電源ライン領域がある場合 (面積が 500mm2 を超える)、局所的に窓を開けるか、グリッド充填 (FILL) として設計する必要があります。図に示すように:
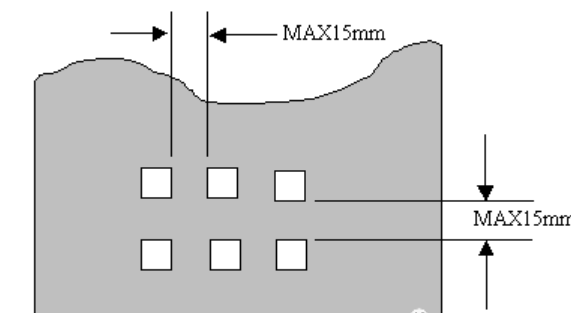
4.3 パッドの製造プロセス要件
4.3.1 スルーホールコンポーネントが接続されていない表面実装コンポーネントの場合、オンラインテスト装置で簡単にテストできるように、テストポイントを追加する必要があり、テストポイントの直径は1.0mm〜1.5mmである必要があります。テストパッドの端から周囲のパッドの端までの距離は少なくとも0.4mmである必要があります。テストパッドの直径は 1mm 以上であり、ネットワーク特性を備えている必要があります。 2.54 つのテスト パッド間の中心距離は 1 mm 以上である必要があります。スルーホールを測定点として使用する場合、スルーホールの外側に直径 XNUMXmm (含む) のはんだパッドを追加する必要があります。
4.3.2 電気接続のある穴がある場所にはパッドを追加する必要があります。すべてのパッドにはネットワーク プロパティが必要であり、接続されたコンポーネントのないネットワークは同じネットワーク名を持つことができません。位置決め穴の中心からテストパッドの中心までの距離は 3mm 以上である必要があります。その他の不規則な形状であるが、溝やパッドなどの電気接続を備えたものは、機械層 1 に均一に配置する必要があります (単一挿入、ヒューズ チューブなどの長穴を指します)。
4.3.3 IC やソケット コネクタなど、ピンの間隔が狭い (ピン間隔が 2.0 mm 未満) コンポーネントの場合、手で挿入されたはんだパッドに接続されていない場合は、テスト パッドを追加する必要があります。テスト ポイントの直径は 1.2 mm ~ 1.5 mm である必要があり、オンライン テスト機器でのテストに適しています。
4.3.4 パッド間の間隔が 0.4 mm 未満の場合は、ウェーブはんだ付け中のはんだブリッジを減らすためにはんだマスクを適用する必要があります。
4.3.5 接着技術を使用した表面実装コンポーネントの場合は、はんだパッドを両端と端に設計する必要があります。はんだの幅は0.5mm、長さは通常2~3mmが推奨です。
4.3.6 片面基板上に手はんだ付けされたコンポーネントがある場合、はんだマスクのスロットは、はんだの波の方向とは反対の方向に開く必要があり、幅は穴のサイズに応じて 0.3 mm から 0.8 mm までの範囲になります。 XNUMXmm;以下の図に示すように:
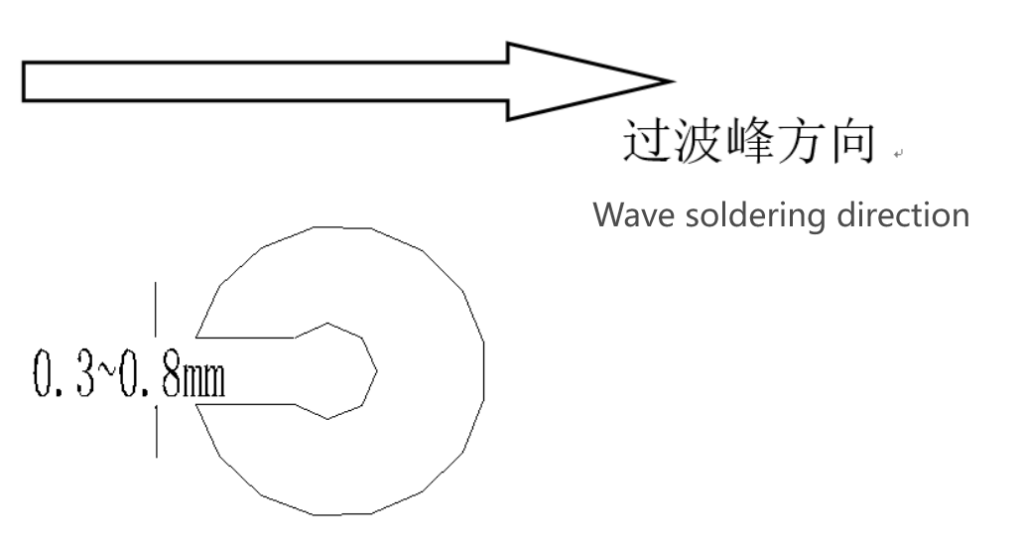
4.3.7 導電性ゴムボタンの間隔とサイズは、導電性ゴムボタンの実際のサイズと一致する必要があります。隣接する PCB 基板は、対応する金めっきの厚さを指定して、ゴールド フィンガーとして設計する必要があります (通常、0.05um ~ 0.015um 以上である必要があります)。
4.3.8 パッドのサイズ、寸法、および間隔は、表面実装コンポーネントの寸法と一致する必要があります。
a.特別な要求がない場合は、部品の穴、パッドの形状、および部品の足の形状が一致している必要があります。穴の中心に対するパッドの対称性を確保し (正方形のコンポーネントのフットは正方形のコンポーネントの穴、正方形のパッドと一致し、円形のコンポーネントのフットは円形のコンポーネントの穴、円形のパッドと一致します)、薄い錫やワイヤの引き抜きを防ぐために隣接するパッドを離しておいてください。
b.同じ回路内の隣接するコンポーネントのフィート、または PIN 間隔が異なる互換性のあるコンポーネントの場合は、個別のパッド穴が必要です。特に互換性のあるリレーパッケージの場合は、互換性のある各パッドを接続する必要があります。 PCB レイアウトの都合上、別々のパッド穴を設定できない場合は、2 つのパッドの周囲をソルダーレジストで囲む必要があります。
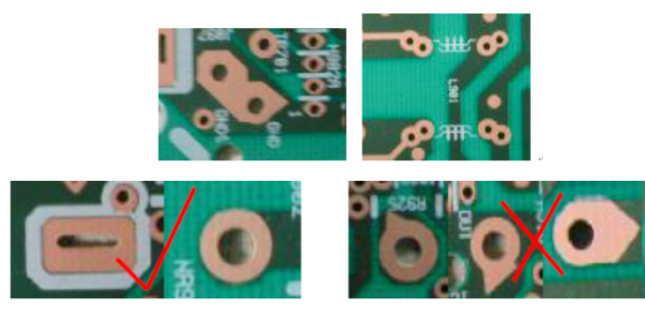