4.3.9 多層基板を設計するときは、プラグインパッケージ内にあり、プリント回路基板と接触する金属ケースを備えたコンポーネントに注意を払う必要があります。最上層のパッドを開けてはなりません。これらは、緑色のオイルまたはシルクスクリーン インク (XNUMX ピン クリスタル、XNUMX ピン LED など) で覆われている必要があります。
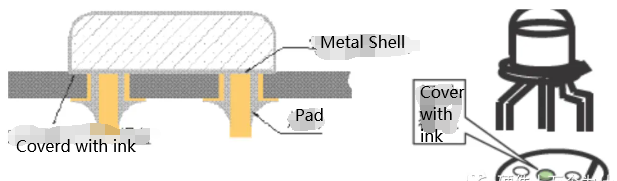
4.3.10 PCB を設計およびレイアウトするときは、強度への影響を避けるために、プリント基板のスロットと穴を最小限に抑えるようにしてください。
4.3.11 貴重なコンポーネント: 貴重なコンポーネントを角、端、取り付け穴、スロット、配電盤の切断端、またはコーナーに置かないでください。これらの位置はプリント基板の高応力領域であり、はんだ接合部やコンポーネントに亀裂や破損が発生しやすくなります。
4.3.12 プリント基板の強度や変形への影響を避けるため、重量部品(変圧器など)は位置決め穴から遠く離れてはいけません。レイアウトするときは、より重いコンポーネントを PCB の下に配置する必要があります (また、最後にウェーブはんだ付けを行う側)。
4.3.13 変圧器やリレーなどのエネルギーを放出するデバイスは、動作中の信頼性への影響を避けるために、アンプ、マイクロコントローラー、クリスタル、リセット回路などの干渉を受けやすいデバイスや回路から遠ざける必要があります。
4.3.14 QFP パッケージの IC (ウェーブはんだ付けプロセスが必要) の場合、IC は 45 度の角度で配置され、はんだパッドが含まれている必要があります (画像を参照)。
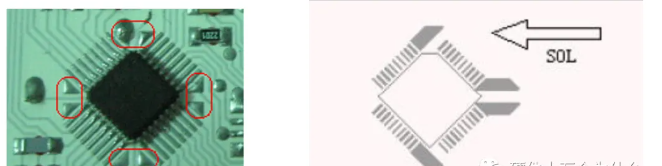
4.3.15 表面実装部品をウェーブはんだ付けする場合、ウェーブ 1 (妨害波) からのはんだが浸入するのを防ぐために、挿入されたコンポーネント (ヒートシンク、トランスなど) の周囲および下に放熱穴を開けてはなりません。上基板上の部品や部品ピンに付着し、後工程の組立時に異物の原因となります。
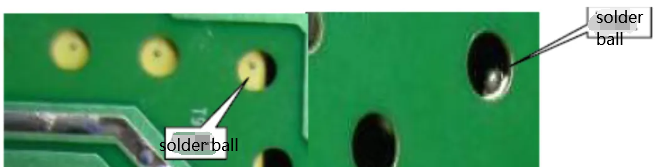
4.3.16 大面積の銅箔では、パッドに絶縁テープを接続する必要があります。
はんだの浸透を良好にするには、大面積銅箔上のコンポーネントのパッドを絶縁テープでパッドに接続する必要があります。 5Aを超える電流が必要なパッドには絶縁パッドは使用できません。 (画像参照)

4.3.17 リフローはんだ付け後のデバイスの位置ずれやトゥームストーンを回避するには、0805 以下の表面実装コンポーネントの両端の熱放散の対称性を確保する必要があります。上の図に示すように、パッドとプリント導体の間の接続幅は 0.3 mm を超えてはなりません (非対称パッドの場合)。
4.4 コンポーネントライブラリの選択要件
4.4.1 既存の PCB コンポーネント パッケージ ライブラリの選択が正しいことを確認する必要があります。
PCB 上の既存のコンポーネント ライブラリでコンポーネントを選択する場合は、パッケージがコンポーネントの物理的形状、ピンの間隔、穴の直径などと一致していることを確認する必要があります。
スルーホール コンポーネントの場合、コンポーネントのピンとスルーホールの間の公差が十分に一致している必要があり (スルーホールの直径がピンの直径の 8 ~ 20 ミルより大きい)、公差を適切に大きくして良好な状態を保証できます。はんだの浸透。特別な要求がない場合、手挿入部品のスルーホールの仕様は次のとおりです。
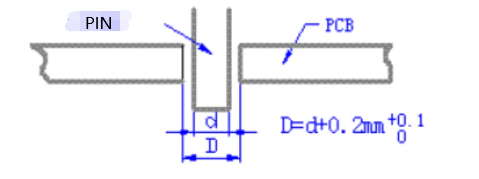
4.4.2 コンポーネントの直径はシリアル化する必要があり、5 mil を超える場合は 40 mil ずつ増加し、つまり 40 mil、45 mil、50 mil、55 mil となり、4 mil 未満の場合は 40 mil ずつ減少、つまり 36 mil、32 mil となります。 、28ミル、24ミル、20ミル、16ミル、12ミル、8ミル。
4.4.3 デバイスのピン径とプリント基板のパッド穴径、プラグピンおよびリフローはんだ付けのはんだパッド穴径の対応は以下のとおりです。
デバイスピン径 (D) | PCB パッド穴径/THT リフローはんだ付けパッド穴径) |
D≦1.0mm | D+0.3mm/+0.15mm |
1.0mm | D+0.4mm/0.2mm |
D>2.0mm | D+0.5mm/0.2mm |
コンポーネント パッケージ ライブラリを作成するときは、穴直径の単位を帝国単位 (ミル) に変換し、穴直径がシリアル化要件を満たしている必要があります。
4.4.4 パッド形状の設計:
4.4.4.1 原則として、コンポーネントパッドの設計は次の点に従う必要があります。
4.4.4.1.1 パッドの方向が流れの方向に対して垂直になるようにしてください。
4.4.4.1.2 パッドの幅は、コンポーネントの幅と等しいか、わずかに大きいことが好ましい。パッドの長さはパッドの幅よりわずかに小さくなります。
4.4.4.1.3 コンポーネントのパッド間のギャップを増やすことは、組み立てに有利です。小さめのパッドをお勧めします。
4.4.4.1.4 MT コンポーネントのパッド上またはパッド付近にスルーホールがあってはなりません。そうしないと、リフローはんだ付け時にパッド上のはんだがスルーホールに沿って流れ、仮想はんだ、はんだ不足が発生し、基板の反対側に流れてショートする可能性があります。
4.4.4.1.5 パッドの両端のトレースは均一であるか、同様の熱容量を持っている必要があります。
4.4.4.1.6 パッドのサイズは対称でなければなりません。
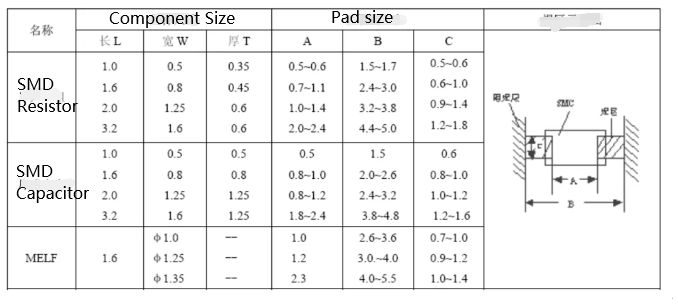
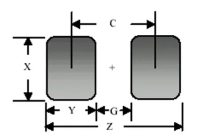
4.4.4.2 チップ部品のはんだパッド形状の設計 (上図を参照): チップ部品のはんだパッドの一般的な設計寸法は、以下の表に示すとおりです。対応するソルダー レジスト フィルムを各パッドの外側に設計できます。ソルダーレジスト膜の目的は、はんだ付け時のはんだブリッジを防止することです。
受動部品のはんだパッド設計の寸法 – 抵抗、コンデンサ、インダクタ (下の表を参照、上の画像と表も参照してください)
パーツ | Z(mm) | G(mm) | X(mm) | Y(参照) | |
チップ抵抗器とコンデンサ | 0201 | 0.76 | 0.24 | 0.30 | 0.26 |
0402 | 1.45〜1.5 | 0.35〜0.4 | 0.55 | 0.55 | |
0603 | 2.32 | 0.72 | 0.8 | 1.8 | |
R0603 | 2.4 | 0.6 | 1.0 | 0.9 | |
L0603 | 2.32 | 0.72 | 0.8 | 0.8 | |
0805 | 2.85 | 0.75 | 1.4 | 1.05 | |
R0805 | 3.1 | 0.9 | 1.6 | 1.1 | |
L0805 | 3.25 | 0.75 | 1.5 | 1.25 | |
1206 | 4.4 | 1.2 | 1.8 | 1.6 | |
1210 | 4.4 | 1.2 | 2.7 | 1.6 | |
1812 | 5.8 | 2.0 | 3.4 | 1.9 | |
1825 | 5.8 | 2.0 | 6.8 | 1.9 | |
2010 | 6.2 | 2.6 | 2.7 | 1.8 | |
2512 | 7.4 | 3.8 | 3.2 | 1.8 | |
3216(タイプA) | 4.8 | 0.8 | 1.2 | 2.0 | |
タンタルコンデンサ | 3528(タイプB) | 5.0 | 1.0 | 2.2 | 2.0 |
6032(タイプC) | 7.6 | 2.4 | 2.2 | 2.6 | |
7343(タイプD) | 9.0 | 3.8 | 2.4 | 2.6 | |
2012(0805) | 3.2 | 0.6 | 1.6 | 1.3 | |
3216(1206) | 4.4 | 1.2 | 2.0 | 1.6 | |
3516(1406) | 4.8 | 2.0 | 1.8 | 1.4 | |
5923(2309) | 7.2 | 4.2 | 2.6 | 1.5 | |
2012チップ(0805) | 3.0 | 1.0 | 1.0 | 1.0 | |
インダクタ | 3216チップ(1206) | 4.2 | 1.8 | 1.6 | 1.2 |
4516チップ(1806) | 5.8 | 2.6 | 1.0 | 1.6 | |
2825Prec(1110) | 3.8 | 1.0 | 2.4 | 1.4 | |
3225Prec(1210) | 4.6 | 1.0 | 2.0 | 1.8 | |
受動部品のはんだパッド設計寸法:
成分 | 長さ(mm) | 幅(mm) |
---|---|---|
抵抗 | 0.9 – 1.3 | 0.4 – 0.7 |
0.9 – 1.3 | 0.4 – 0.7 | |
誘導子 | 0.9 – 1.3 | 0.4 – 0.7 |
具体的な設計寸法と構成については、上の画像と表を参照してください。
4.4.4.3 SOP、QFP はんだパッド設計: SOP、QFP はんだパッドのサイズは、IPC-SM-782 に従って設計できます。
SOP、QFP はんだパッドの設計基準については (以下の表を参照):
はんだパッドのサイズは、コンポーネントのサイズに応じて決定する必要があります。最適なはんだ付け効果を得るには、はんだパッドの幅 = ピン幅 + 2 * ピンの高さになります。はんだパッドの長さは図 L2 に示されています (L2 = L + b1 + b2; b1 = b2 = 0.3mm + h; h = コンポーネント ピンの高さ)
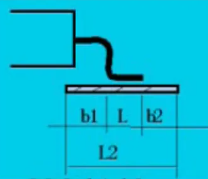
4.4.4.4 特別な要件がない場合、スルーホール実装コンポーネントのはんだパッドの仕様は次のとおりです。
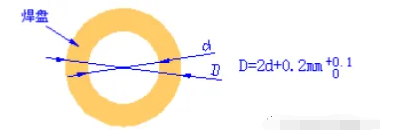
4.4.4.5 ピン間隔 2.0mm 以下の手挿入 PIN、コンデンサなどの場合、はんだパッドの仕様は次のとおりです。 ① 多層基板のはんだパッド径 = 穴径 + 0.2~0.4mm。 ② 単層基板のはんだパッド径=2×穴径
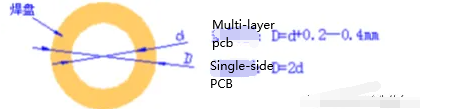
4.4.4.6 一般的な表面実装 IC はんだパッドの設計、添付ファイルを参照してください (以下の図は一部を抜粋したものです。具体的な寸法については添付ファイルを参照してください)
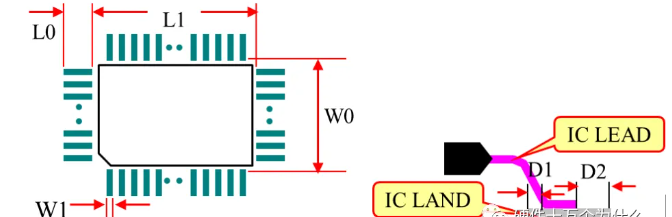
4.4.5 新しいデバイス PCB コンポーネント パッケージ ライブラリが正しく確立される必要がある
4.4.5.1 PCB 上に既存のコンポーネント パッケージ ライブラリがないデバイスは、デバイス データに基づいて新しいコンポーネント パッケージ ライブラリを確立し、シルクスクリーン インベントリが物理的オブジェクト、特に新しく確立された電磁コンポーネント、自作の構造コンポーネントなどと一致することを確認する必要があります。 、コンポーネント ライブラリとデータ (確認書、仕様書、図面) を照合します。新しいデバイスは、さまざまなプロセス要件 (リフローはんだ付け、ウェーブはんだ付け、スルーホール リフローはんだ付け) を満たすことができるコンポーネント ライブラリを確立する必要があります。
4.4.5.2 ウェーブはんだ付けが必要な SMT コンポーネントは、表面実装ウェーブはんだ付けパッド ライブラリを使用する必要があります。
4.4.5.3 コンポーネントの成型および取り付けツールを減らすために、軸コンポーネントおよびジャンパー ピンの種類を最小限に抑える必要があります。
4.4.5.4 異なる PIN 間隔と互換性のあるコンポーネントには、個別のはんだパッド穴が必要です。特に、カプセル化リレーと互換性のあるはんだパッドを接続する必要があります。
4.4.5.5 表面実装部品は手はんだ付け時の熱衝撃により損傷しやすいため、手はんだ付けのデバッグ コンポーネントとして使用しないでください。
4.4.5.6 実験による検証が問題なく行われない限り、PCB と熱膨張係数が大きく異なる表面実装部品は、はんだパッドの層間剥離を引き起こす可能性があるため、選択すべきではありません。
4.4.5.7 実験による検証が問題なく行われない限り、非表面実装部品を表面実装部品として使用すべきではありません。これには手作業によるはんだ付けが必要になる場合があり、効率と信頼性が低下します。
4.4.5.8 多層 PCB の場合、はんだ付けピンとしての側面の局所的な銅めっきは、銅めっきの接着強度を高めるために各層が銅箔で接続されていることを確認する必要があります。同時に実験による検証も問題なく行わなければなりません。そうしないと、両面基板の側面銅メッキをはんだ付けピンとして使用できなくなります。
4.4.6 ウェーブはんだ付け時の影の影響を防ぐために、ウェーブはんだ付けを必要とする片面バックボード コンポーネントの安全距離。SMT コンポーネント間の距離は、次の要件を満たす必要があります。
- 同じ種類のコンポーネント間の距離 (図に示すように)
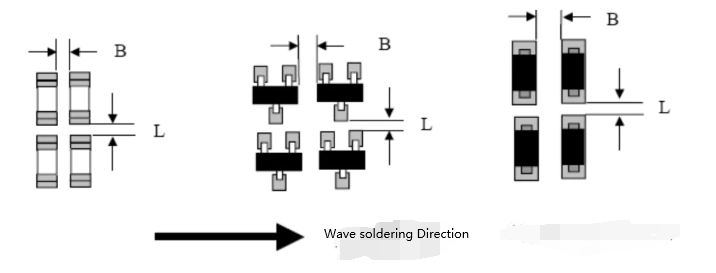
4.6.1 同じタイプの SMD コンポーネントの間隔は 0.3mm 以上、異なるタイプのコンポーネント間の間隔は 0.13*h+0.3mm 以上である必要があります (注: h は XNUMX つの異なる部品間の最大高さの差を指します)。 、THT コンポーネントの間隔は、操作と交換を容易にする必要があります。
4.6.2 実装部品のはんだパッドの外側と隣接する実装部品の外側との間の距離は 2mm より大きくなければなりません。
4.6.3 SMD コンポーネントは、コネクタの挿入および取り外し時のコンポーネントへの応力損傷を防ぐために、頻繁に差し込まれるコンポーネントまたはボードエッジコネクタの周囲 3mm 以内で避ける必要があります。
4.6.4 位置決め穴の中心から表面実装部品の端までの距離は 5.0mm 以上である必要があります。
4.6.5 0805 パッケージを超えるセラミック コンデンサは、伝送エッジの近くまたは応力の少ない領域に配置する必要があり、その軸方向は基板の入口方向と平行である必要があり、1825 を超えるセラミック コンデンサはできるだけ避ける必要があります。可能。 (保留されたコメント)
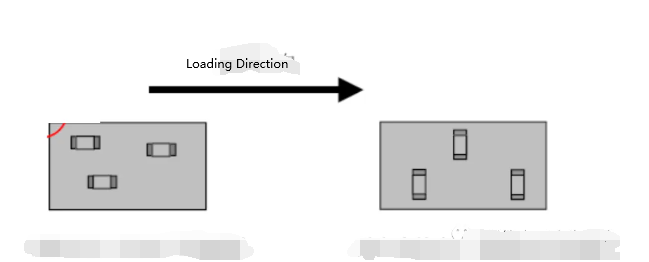
4.4.6.6 コネクタの挿入および取り外し時のコンポーネントへの応力による損傷を防ぐために、頻繁に差し込まれるコンポーネントまたはボードエッジコネクタの周囲に SMD を 3mm 以内に配置しないようにする必要があります。図を参照してください:
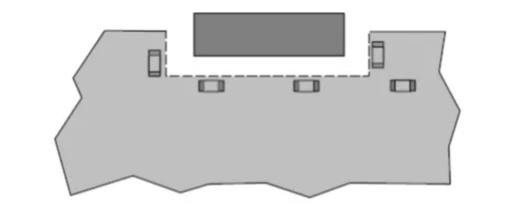
4.4.6.7 ウェーブはんだ付け用の表面実装コンポーネントは、スタンドオフの指定要件を満たしている必要があります。ウェーブはんだ付け用の表面実装コンポーネントのスタンドオフは 0.15mm 未満である必要があります。それ以外の場合は、ウェーブはんだ付けの場合は B 側に配置しないでください。コンポーネントのスタンドオフが 0.15 mm ~ 0.2 mm の場合、銅箔をコンポーネント本体の下に配置して、コンポーネントの底部と PCB の表面の間の距離を減らすことができます。
4.4.6.8 ウェーブはんだ付け中のスルーホールはんだ点の最小安全距離は、ウェーブはんだ付け中にはんだ付け点がブリッジしないように決定されており、背面テスト ポイントの端の間の距離は 1.0 mm より大きくなければなりません。
4.4.6.9 ウェーブはんだ付けが必要なスルーホールコンポーネントのはんだパッド間の間隔は、ウェーブはんだ付け中にはんだ点がブリッジしないように、1.0 mm 以上である必要があります (コンポーネントピンのはんだパッドの端の間の間隔を含む)。スルーホールコンポーネントピンの好ましいピッチ(ピッチ)は≧2.0mmです
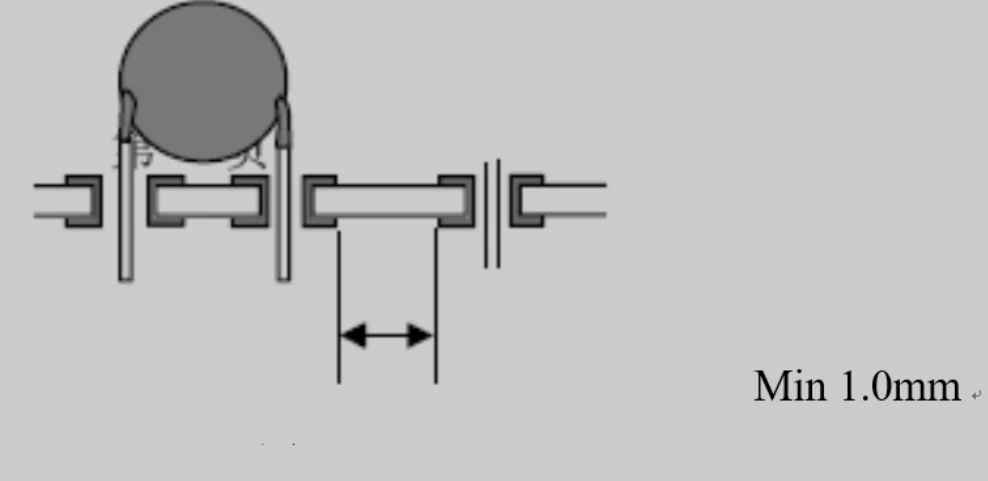
4.4.6.10 プラグイン コンポーネントの 0.6 行あたりのピンが多数あり、コンポーネントが PCB 挿入方向に平行なはんだパッドで配置されている場合、隣接するはんだパッド エッジの間隔を 1.0 ~ XNUMX mm にする推奨アプローチは、楕円形を使用することです。の形のはんだパッド、または錫めっきパッドを追加します。
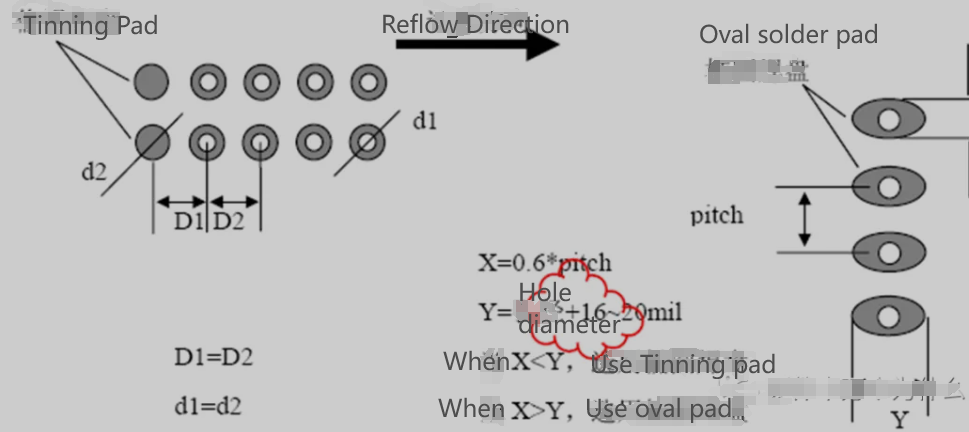
4.4.6.11 表面実装コンポーネント間の最小間隔は、次の要件を満たす必要があります。
機械の配置の場合:
- 同種部品間:≧0.3mm
- 異なるタイプのコンポーネント間: ≥ 0.13 * h + 0.3mm (h は隣接するコンポーネント間の最大高さの差)
手動配置の場合:
- 部品間: ≥ 1.5mm。
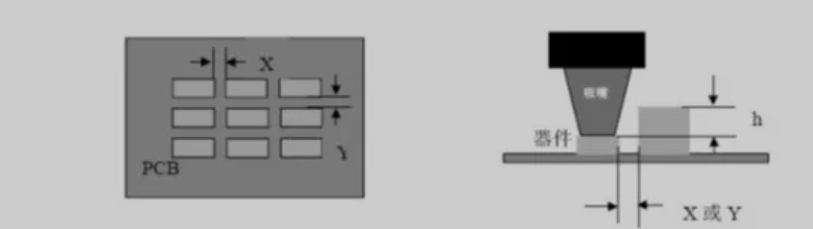
4.4.6.12 コンポーネントの外端から基板トラックの端までの距離は 5mm 以上である必要があります。これは、ウェーブはんだ付けやリフローはんだ付けの際に、コンベアトラックの爪が部品に触れないようにするためです。この要件が満たされない場合は、PCB にエッジ処理を施し、コンポーネントと V-CUT の間の距離を 1mm 以上にする必要があります。
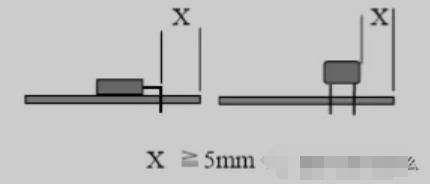
4.4.6.13 デバッグやメンテナンスのために、調整可能でプラグイン可能なコンポーネントの周囲に適切なスペースを確保する必要があります。調整可能なコンポーネントの向きとプラグイン可能なコンポーネント用に確保されるスペースは、PCBA の取り付けレイアウトと調整可能なコンポーネントのデバッグ方法に基づいて決定する必要があります。
4.4.6.14 すべてのプラグイン磁気コンポーネントには頑丈なベースが必要であり、ベースのないプラグイン インダクタの使用は禁止されています。
4.4.6.15 有極トランスのピンを対称に設計することは避けてください。ピンが回路に接続されていない場合は、はんだ付け強度を高めるためにはんだパッドを追加してください。
4.4.6.16 取り付け穴の禁止領域にはコンポーネントやトレースを配置しないでください (取り付け穴自体のトレースと銅箔を除く)。
4.4.6.17 金属ケースのコンポーネントと他のコンポーネントの間の距離は、安全規制を満たしている必要があります。金属ケースのコンポーネントの配置では、他のコンポーネントからの距離が安全規制を満たすようにする必要があります。
4.4.6.18 スルーホールリフローはんだ付けを使用したコンポーネントのレイアウトの要件:非搬送エッジ サイズが 300mm を超える PCB の場合、はんだ付け中の PCB 変形に対する挿入コンポーネントの重量の影響や、コンポーネントへの挿入コンポーネントの影響を軽減するために、PCB の中央に重いコンポーネントを配置することは避けてください。すでにボード上に配置されています。 b.挿入を容易にするために、コンポーネントは挿入操作の側面近くに配置する必要があります。 c.長いコンポーネント (メモリ カード ソケットなど) の場合、長さ方向は搬送方向と一致している必要があります。コンポーネントの複数のピンが同じ直線上にある場合、コネクタ、DIP パッケージ コンポーネント、および T220 パッケージ コンポーネントは、それらの軸がウェーブはんだ付けの方向と平行になるように配置する必要があります。ダイオードや 1/4W 抵抗器などの軽量部品は、その軸がウェーブはんだ付けの方向と直角になるように配置する必要があります。これにより、一方の端が他方の端より先に固化することによるウェーブはんだ付け中の浮きが防止され、スルーホールコンポーネントに四角いはんだパッドを使用することがなくなります(はんだ付け不良やブリッジングの原因となる可能性があります)。