편집자 주: 최신 고속 설계에서는 신호 무결성, 전력 무결성 및 EMC를 개별적으로 분석하는 것만으로는 충분하지 않습니다. 성공적인 설계를 위해서는 전체적인 접근 방식이 필수적입니다.
배경 문제: 신호가 레이어의 인접한 참조 평면 사이의 분할 영역을 교차할 때 신호 무결성에 대한 논의가 자주 발생합니다. 어떤 사람들은 신호가 누화 및 EMC 문제를 증가시킬 수 있으므로 분할을 넘어서는 안 된다고 주장하는 반면, 다른 사람들은 레이어 스택업과 전력/접지 평면의 분할 간격 너비를 신중하게 설계하면 문제가 없어야 한다고 제안합니다. 그렇다면 올바른 접근 방식은 무엇입니까? 물론 가장 좋은 대답은 “상황에 따라 다릅니다!”입니다. 이 기사에서는 신호가 분할된 평면을 통과할 때의 시나리오를 살펴봅니다.
먼저, 전형적인 것을 생각해 보자. 4층 PCB 총 두께가 62mil인 스택업. 표면 레이어는 신호 레이어이고 내부 레이어는 평면 레이어입니다. 트레이스 폭은 7/8mil이고 차동 임피던스는 100Ω이고 단일 종단 임피던스는 56Ω입니다.
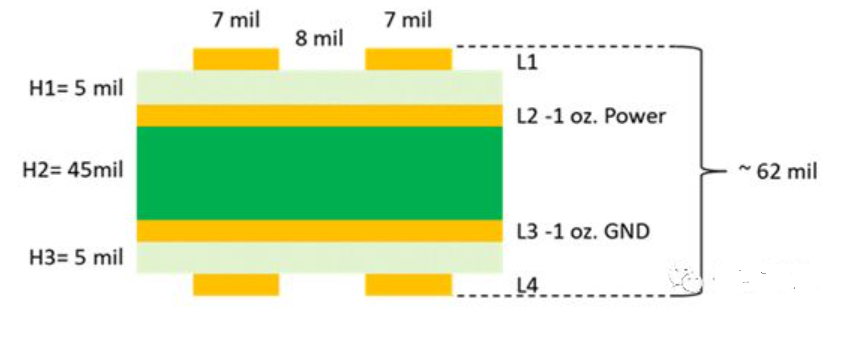
현대 전자 제품 설계에서는 제품에 여러 개의 전원 레일을 갖는 것이 매우 일반적입니다. 이는 4층 보드의 전원 평면이 필연적으로 분할된다는 것을 의미합니다. 따라서 라우팅 중에 분할을 통한 신호 교차의 존재는 불가피합니다.
그림과 같이 인접한 층 사이의 50mm 폭의 간격을 가로지르는 한 쌍의 표면 전송 선로를 가정하면 간격을 통과하기 전과 후의 마이크로스트립 라인의 단면이 표시됩니다. 표면에서 인접한 전력 기준층까지의 유전체 두께 H1이 고려됩니다. 갭에 인접한 전원 기준 평면이 없고 다음 기준 평면은 하단 레이어에 인접한 접지이므로 갭의 유전체 두께는 H1에 1oz 전원 레이어의 두께를 더한 값과 다음 유전체 레이어를 더한 값과 같습니다. H2. 전력층의 두께가 1.2mil이면 갭의 전체 유전체 두께는 51.2mil입니다.
이 토폴로지의 100차 근사치는 두 개의 서로 다른 임피던스를 갖는 세 개의 전송선 세그먼트의 조합입니다. 첫 번째와 마지막 세그먼트는 모두 56ohm 차동 임피던스와 134ohm 단일 종단 임피던스이며, 갭 부분의 전송 라인은 103ohm의 차동 임피던스와 3ohm의 단일 종단 임피던스를 갖습니다. 임피던스가 다른 부품보다 높아서 여기에서 신호 반사가 발생합니다. 반사의 높이와 폭은 해당 신호 상승 시간과 간격 구조의 함수입니다. 상승 시간이 빠르고 간격이 넓을수록 반사가 더 많이 발생합니다. 그림 XNUMX은 시뮬레이션 결과를 보여줍니다.
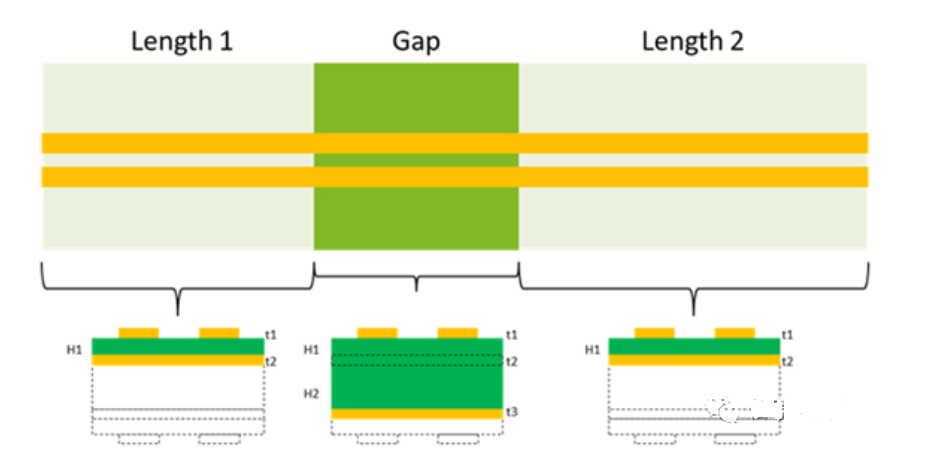
전송선의 첫 번째 및 세 번째 세그먼트는 TLines-LineType(ADS)의 2D 모델을 사용하여 시뮬레이션하고, 간격의 전송선은 3D 전자기장 솔버(Momentum 또는 EMPro)를 사용하여 시뮬레이션하여 전자기장 효과를 얻습니다. 신호가 통과됩니다. 유전체 재료는 동일합니다. S-파라미터가 추출되어 회로도에 사용됩니다.
토폴로지의 전체 길이는 2.65인치이며, 전송선(L1)의 첫 번째 세그먼트 길이는 500mil이고 세 번째 세그먼트(L2)의 길이는 2인치입니다. 3D 부품은 각각 50mil의 XNUMX개 세그먼트로 분할되어 총 길이가 변경되지 않도록 하면서 간격 너비를 쉽게 조정할 수 있습니다.
간격 크기의 효과를 비교하기 위해 두 가지 간격 너비가 사용됩니다. 전원 플레인 사이에 50mil의 간격이 있는 것이 일반적이며 최악의 시나리오를 나타냅니다. 5mil 간격이 최적의 시나리오이며 전송선에서 납땜 패드까지의 일반적인 최소값이기도 합니다.
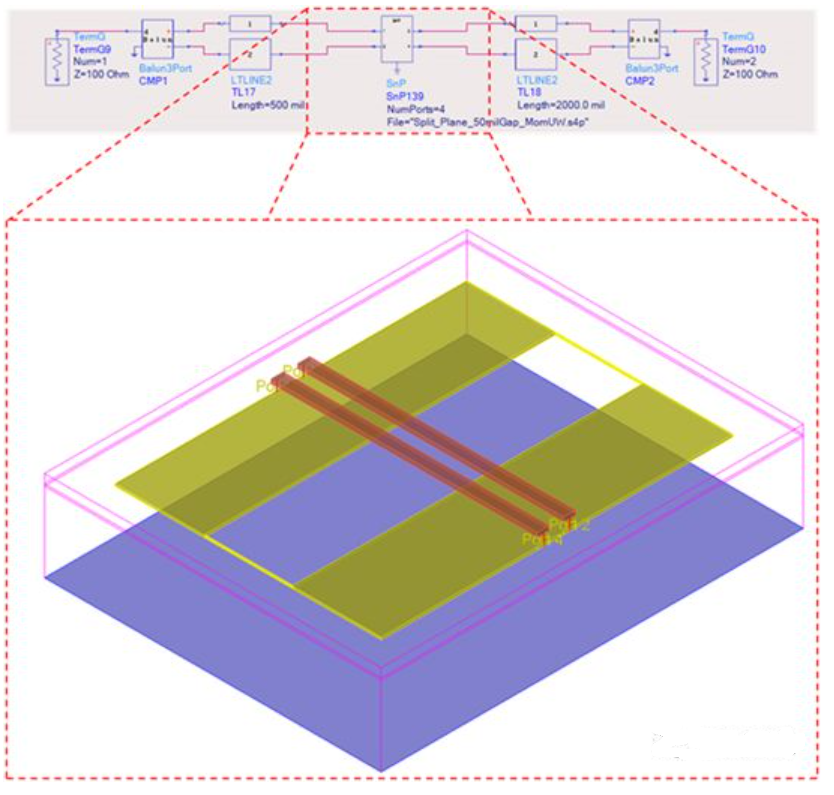
차동 여기 소스가 포트 1에 적용되고 차동 임피던스의 비교가 그림 4에 나와 있습니다. 포트 2의 임피던스를 쉽게 볼 수 있도록 발룬 변환기를 사용하여 포트 4를 포트 2로 변환합니다. 빨간색 곡선은 결과를 나타냅니다. 50mil 갭의 경우 5mil 갭(파란색 곡선)에 대한 결과에 비해 더 높은 임피던스 불연속성을 나타냅니다. 이는 방출된 펄스의 높이가 상승 시간과 간격 폭에 의해 결정되기 때문입니다. 상승 시간은 간격 폭에 비해 공간 길이가 더 작기 때문에 상승 시간을 변경하는 것만으로는 최대 임피던스 불연속성을 달성할 수 없습니다. 이는 아래 시뮬레이션을 통해 보여드리겠습니다.
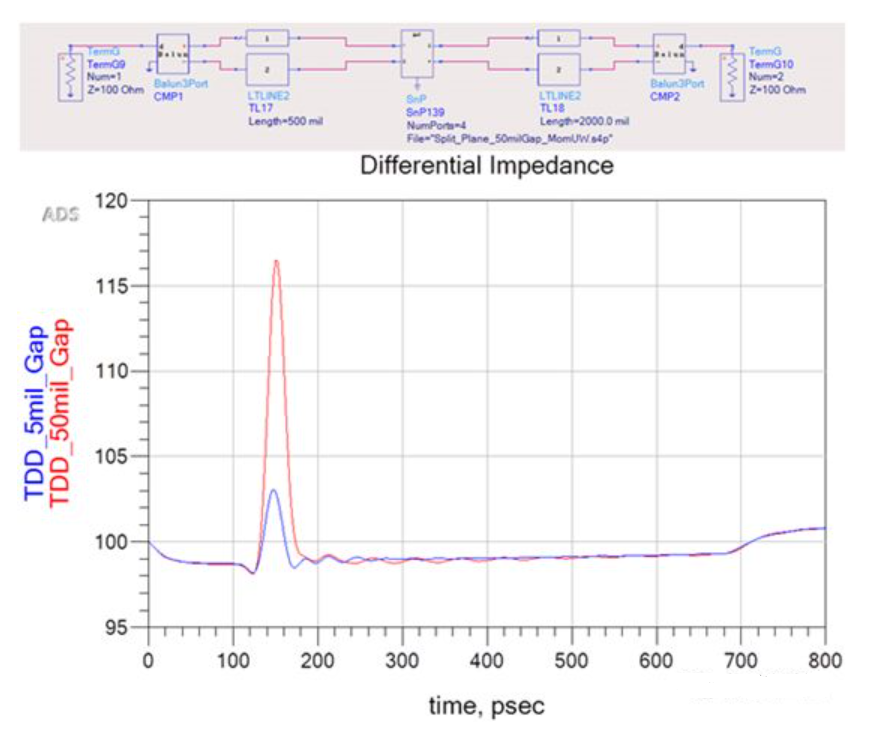
다음 그림과 같이 여기 소스가 2mil 간격으로 포트 50에 적용되고 포트 1의 입력 신호와 비교됩니다. 전송선의 손실과 함께 간격 전 2.05인치의 지연으로 인해 신호 에지가 느려집니다. 예상한 대로 반사의 진폭은 실제로 더 낮습니다.
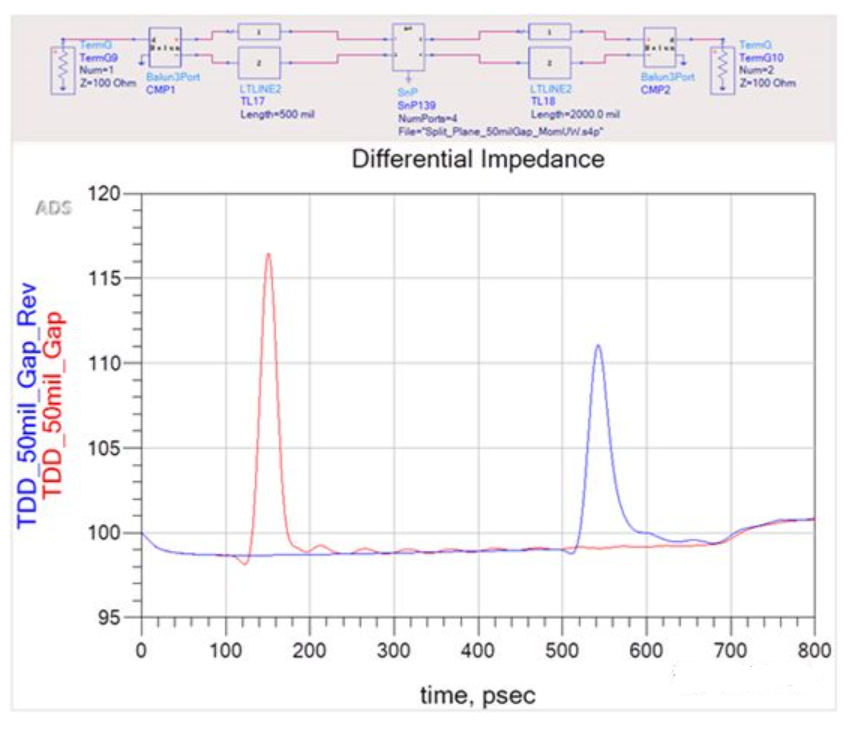
그림에 표시된 것처럼 단일 종단 사례에 대한 분석은 다음과 같습니다. 빨간색 곡선은 50mil 간격을 나타내고 파란색 곡선은 5mil 간격을 나타내며 검은색 곡선은 간격이 없음을 나타냅니다. 상승 시간이 20ps인 경우 갭이 50mil일 때 반사 전압이 가장 높으므로 갭이 없는 경우에 비해 전송 선로 지연이 약간 증가합니다.
세 가지 시나리오 모두에서 일반적인 근단 누화 및 원단 누화 곡선 변화를 관찰할 수 있습니다. 갭을 통한 전송선 간의 긴밀한 결합으로 인해 반사가 더 높아져 근단 누화가 더 커집니다.
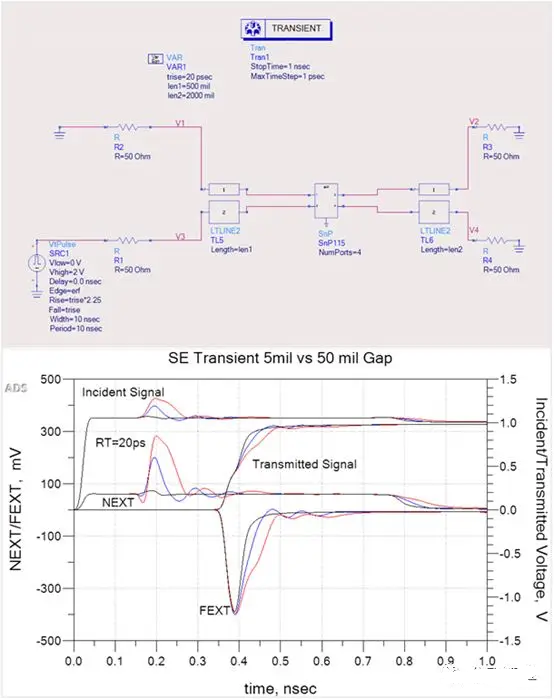
그림에 표시된 것처럼 단일 종단 사례에 대한 분석은 다음과 같습니다. 빨간색 곡선은 50mil 간격을 나타내고 파란색 곡선은 5mil 간격을 나타내며 검은색 곡선은 간격이 없음을 나타냅니다. 상승 시간이 20ps인 경우 갭이 50mil일 때 반사 전압이 가장 높으므로 갭이 없는 경우에 비해 전송 선로 지연이 약간 증가합니다.
세 가지 시나리오 모두에서 일반적인 근단 누화 및 원단 누화 곡선 변화를 관찰할 수 있습니다. 간격을 통과할 때 전송선 간의 긴밀한 결합으로 인해 반사가 더 높아져 근단 누화가 더 커집니다.
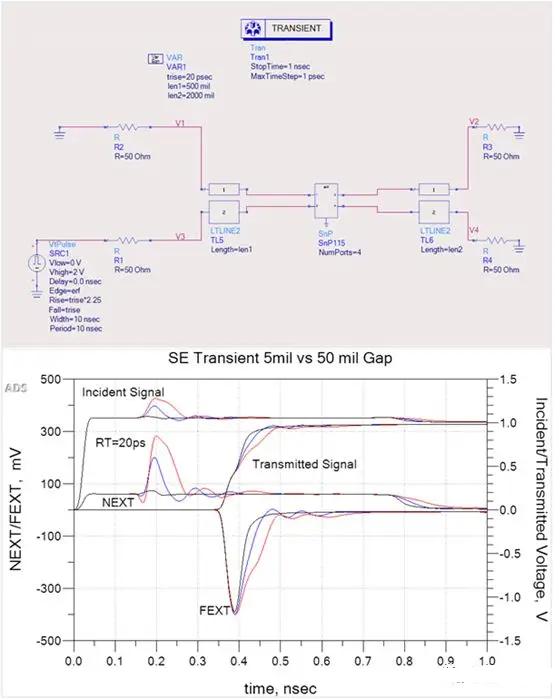
50mil 간격이 있으면 근단 누화 펄스가 크게 증가하는 반면 원단 누화는 약간만 증가합니다. 근단 누화 전압과 달리 원단 누화 전압의 피크 값은 결합 길이에 따라 달라집니다. 특정 시간 지연(TD)에서 진폭은 공격 라인 신호 상승 시간의 약 50%에서 최고조에 이릅니다.
마찬가지로 공격 라인의 신호는 공격 라인에 다시 연결되는 원단 누화 전압에 연결되어 상승 시간에 영향을 줍니다. 공격 라인 맨 끝의 파형은 맨 끝 누화 전압과 원래 신호 전압의 중첩이므로 누화가 발생하지 않습니다. 맨 끝은 소스 끝에서 2.65인치 떨어져 있으므로 맨 끝 누화는 포화 상태에 가까워집니다. 그림 100과 같이 전송선의 마지막 세그먼트 길이를 7mil로 줄이면 원단 누화에 대한 갭의 영향을 더 쉽게 이해할 수 있습니다.
빨간색 곡선은 상승 시간이 7ps인 입력 신호(V20)를 나타내고, 청록색 곡선(V8)은 맨 끝에서 전송된 신호의 파형을 나타내며, 연한 파란색(V5)은 근단 누화를 나타내고, 연한 녹색( V6)은 원단 누화를 나타내고, 진한 녹색(V15)은 TL13를 통과한 후 노드 V44에서의 공격 신호를 나타냅니다. 갭 섹션의 높은 임피던스 특성으로 인해 이 전송 라인 세그먼트에서는 반사 증가로 인한 오버슈트가 나타날 수 있습니다.
주황색 파형(V13)은 V15에서 공격 신호의 상승 에지와 일치하는 원단 네거티브 누화 펄스를 보여줍니다. 근단 누화는 V15의 포지티브 반사와도 일치합니다. 공격 신호가 갭을 통과할 때 지연을 경험함에 따라 반사의 추가 전압 스윙은 원단 누화 펄스의 진폭을 증가시키고 반전된 모양은 짙은 녹색 파형에서 볼 수 있듯이 반사된 펄스의 모양을 반영합니다. V14), 그러면 공격 신호에 다시 결합되어 자홍색 곡선(V16)으로 표시된 것처럼 결합 섹션을 떠날 때까지 상승 시간이 감소합니다.
이 기사에서 다루는 문제는 신호가 분할된 평면을 통과할 때 전송된 신호가 임피던스 불일치로 인해 양극 및 음극 반사를 겪으며 반사 시간은 간격을 통과하는 데 걸리는 시간과 동일하다는 것입니다. 이는 신호의 진폭과 원단 누화 펄스를 증가시켜 원단 누화의 파형에 비례하여 전송된 신호의 상승 시간을 늦춥니다.
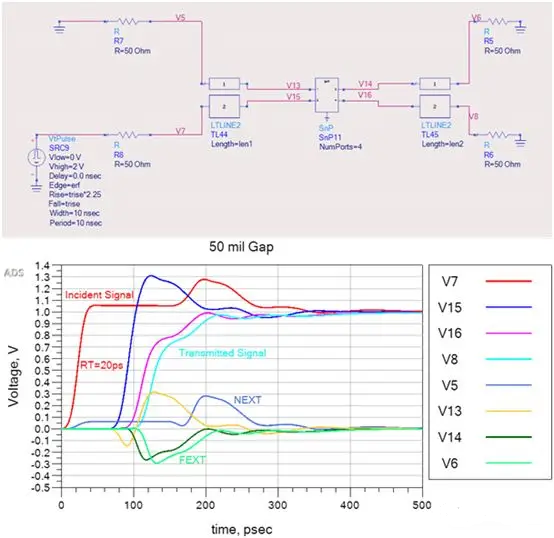
분할된 평면과 가장자리의 여러 복귀 경로를 고려하여 효과적인 슬롯 안테나가 형성되어 소음을 외부로 방출합니다. EMI FCC 클래스 B 방사 요구 사항(3미터 필드)을 충족하려면 방사 잡음이 100~30MHz에서 80mV/m 미만, 200MHz~216GHz에서 1mV/m 미만이어야 합니다.
마이크로스트립 라인이 분할된 평면을 통과할 때 불연속적인 복귀 경로와 차폐 부족으로 인해 노이즈가 자유 공간으로 방출될 수 있습니다. 인접한 기준 평면 사이의 간격에서 반환 전류 밀도의 시각화는 3D 시뮬레이션 소프트웨어를 통해 달성할 수 있습니다.
그림 8은 인접한 기준 평면의 단일 종단 신호 반환 전류 밀도를 비교합니다. 왼쪽에서는 4GHz 사인파가 50mil 간격을 통과하고 오른쪽에서는 5mil 간격을 통과합니다. 4GHz 신호를 선택한 이유는 일반적인 8레이어 PCIe 보드에서 3Gbps PCIe Gen 4의 Nyquist 주파수를 나타내기 때문입니다. 포트 1과 2가 적절하게 종단된 상태에서 포트 3에서 포트 4로 신호를 구동하면 분할 시 기준 평면의 반환 전류 밀도 분포를 명확하게 관찰할 수 있습니다.
희생선이 위치한 간격의 가장자리에서 전류 밀도가 약간 증가하는 것을 확인하십시오. 이는 앞서 설명한 것처럼 인접한 라인의 복귀 전류가 추가 원단 누화 전압을 발생시킨다는 것을 나타냅니다. 이러한 관점에서 분할을 교차하는 단일 종단 선은 최적의 접근 방식이 아닐 수 있습니다.
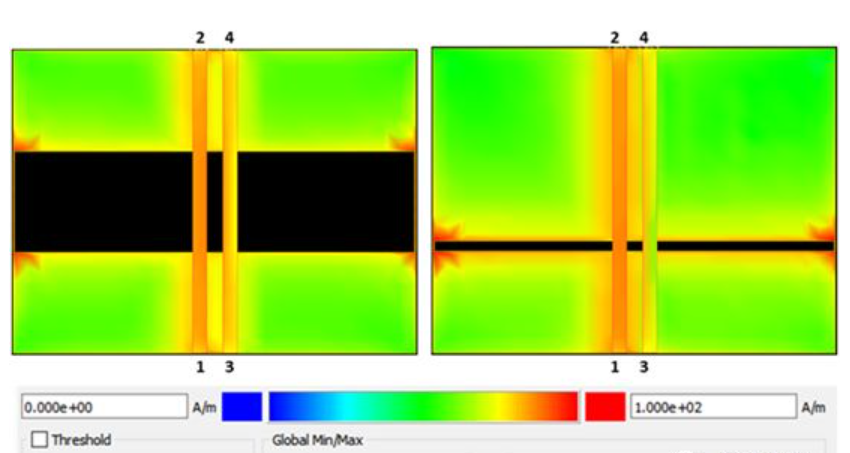
그림 9는 4GHz 차동 신호가 50mil(왼쪽)과 5mil(오른쪽) 간격을 통과할 때 기준 평면의 반환 전류 밀도를 보여줍니다. 두 개의 차동 쌍 사이의 최대 전류 밀도는 분할 가장자리에 집중되어 있으며 작은 부분만이 간격을 따라 전파되는 것을 볼 수 있습니다.
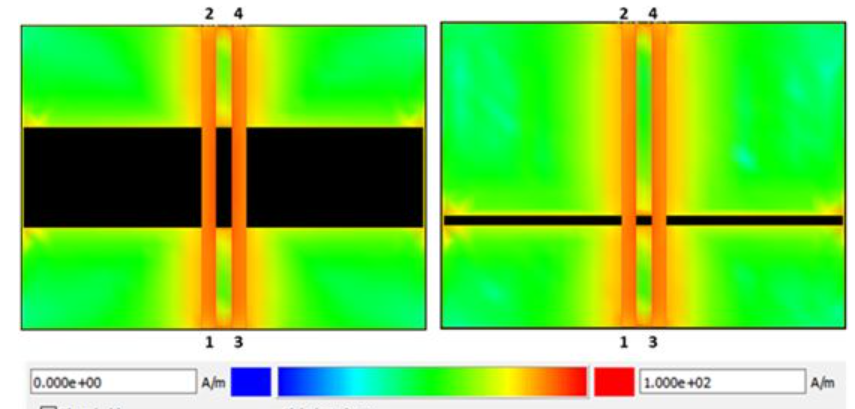
단일 종단 신호가 포트 1에서 포트 2로 입력되고 다른 포트는 종료된 경우 그림 10은 평면 레이어 L2 및 L3의 전류 방향을 표시합니다. 전류 방향이 포트 2에서 포트 1인 경우 L2의 반환 전류는 간격의 맨 끝(포트 1 쪽)에서 두 부분으로 분할되는 것을 볼 수 있습니다. 또한 L3에는 2개의 역회전 전류가 있으며 주로 간격의 왼쪽과 오른쪽 절반에 집중되어 있습니다. 이는 평면 공동에 EM 에너지를 주입하는 L2의 간격 가장자리를 따라 역회전하는 전류로 인해 발생합니다. L3와 LXNUMX의 회전 전류 방향이 반대라는 점은 주목할 만합니다.
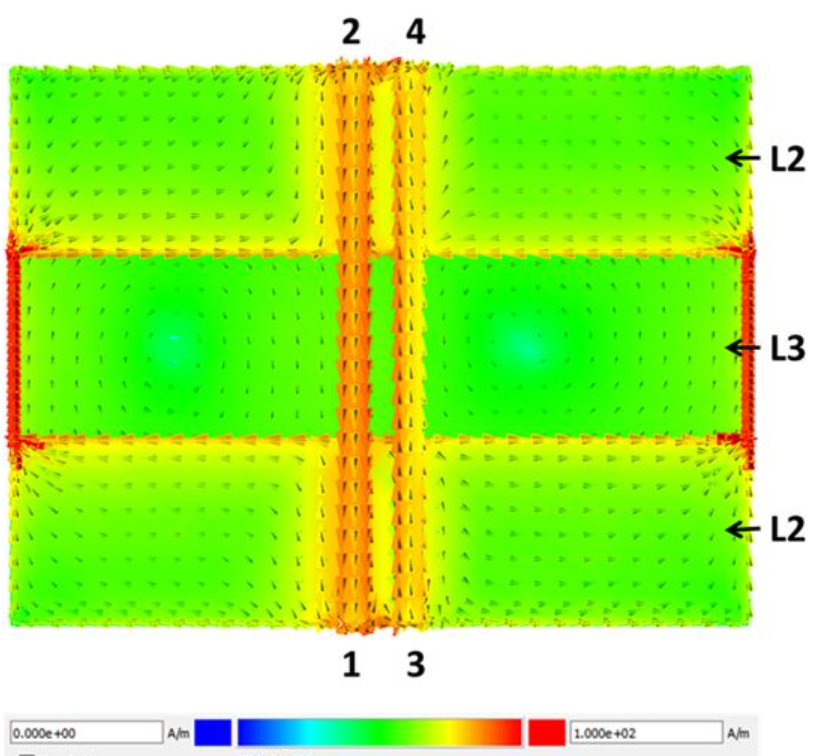
그러나 그림 11과 같이 두 개의 전송선에 차동 신호를 인가하면 간격의 가장자리를 따라 전류의 방향이 동일한 것을 관찰할 수 있습니다. L3의 회전 전류는 단방향이며 차동 쌍과 갭 사이에 집중된다는 점에 유의하는 것도 중요합니다. 여기서 문제는 두 개의 전송선에 차동 신호가 적용되더라도 여전히 전류가 갭의 가장자리로 흐르고 있어 평면 공동에 잡음이 유입되고 자유 공간으로 방사되어 EMI가 발생한다는 것입니다.
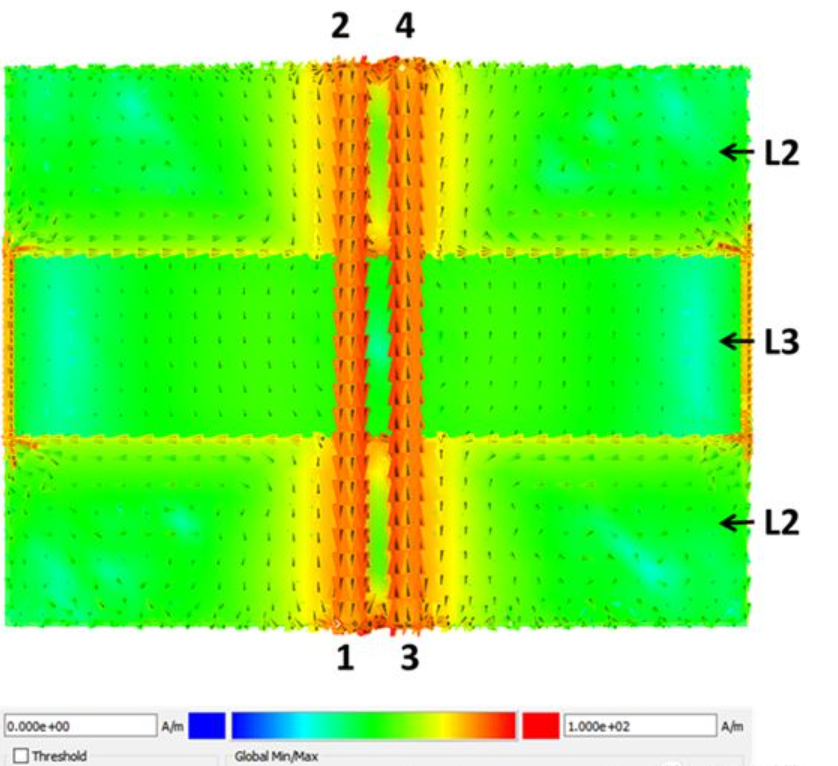
앞선 분석에서는 차동쌍의 예시에서는 완벽한 내부 매칭을 가정했지만 실제로는 그런 경우가 드물다. 동일하지 않은 라우팅 길이, 유리 섬유 효과, 커넥터 핀 길이의 차이 또는 레이어 변경 시 차동 비아의 비대칭성과 같은 요인으로 인해 내부 지연 불일치가 발생할 수 있습니다. 이러한 상황이 발생하면 일부 공통 모드 신호가 차동 모드 신호로 변환될 수 있습니다. 그림 12에 표시된 것처럼 변환 정도는 내부 지연 불일치에 따라 달라집니다. 이상적인 차동 쌍에서 Vdiff는 P 신호와 N 신호 간의 전압 차이를 나타냅니다. 위상차가 180도이면 공통 모드 전압이 두 배가 되어 공통 모드 전압이 발생하지 않습니다. 그러나 스큐가 있는 경우 차동 쌍의 위상차는 180도가 아닙니다. 스큐를 고려하면 차동 신호가 변형되어 공통 모드 전압(Vcom)이 발생합니다. 공통 모드 전압의 크기와 모양은 위상 오프셋에 비례합니다. P와 N의 상이 동일하면 차동전압이 없고 모두 동상전압이 된다. 공통 모드 전압에도 복귀 경로가 필요하며 경로가 중단되면 복귀 전류가 단일 종단 복귀 전류와 유사하게 분할 평면을 통과합니다.
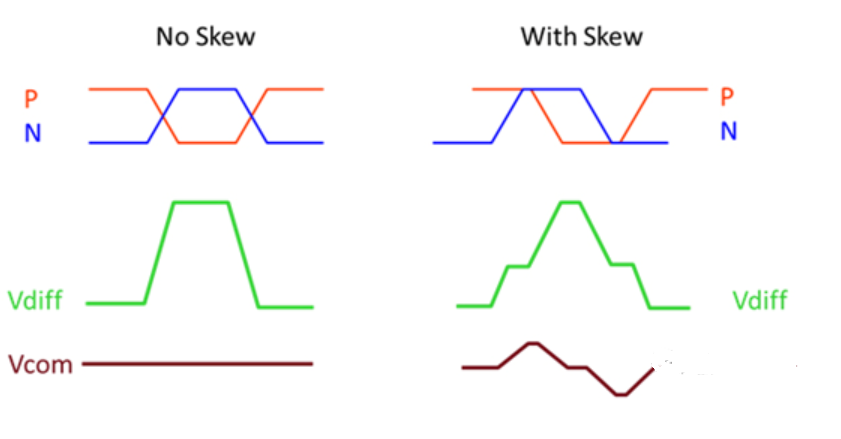
일부 PCIe 배선 사양에 따르면 최악의 스큐는 0.21UI입니다(하나의 UI는 3비트의 시간을 나타냄). PCIe Gen8 0.21Gbps에서 26.3UI 오프셋은 50ps에 해당합니다. 13mil 간격을 통과하는 시나리오는 이상적인 상황과 비교하여 그림 8에 표시된 내부 위상 변화와 동일합니다. 예상한 대로 공통 모드 전압은 파티션 평면을 통과하고 공통 모드 복귀 전류는 단일 종단 라인이 파티션 평면을 통과하는 상황과 유사합니다(그림 100). 유일한 차이점은 XNUMX% 공통 모드 전류가 없으므로 차동 모드 반환 전류도 있다는 것입니다.
해결해야 할 마지막 문제는 인접한 접지 층과 분할된 전력 층 사이에 극도로 얇은 유전체 층이 있는 경우 분할된 층을 통과할 때 더 나은 복귀 경로 역할을 한다는 것입니다. 논리적으로 이는 전송 라인과 분할된 기준 평면 사이의 유전체 두께가 증가함에 따라 전송 라인의 임피던스가 감소하므로 신호 무결성의 관점에서 볼 때 의미가 있습니다.
이전 예에서는 두께가 62mil인 6층 보드를 가정했습니다. 이는 스택의 내부 층 유전체의 두께를 거의 결정합니다. 참조 평면을 전원 평면 사이의 간격에 더 가깝게 이동하려면 스택 대칭과 전체 두께를 유지하기 위해 PCB 레이어 수를 최소 XNUMX개 레이어로 늘려야 합니다.
갭 아래의 유전체 두께를 줄여 5mil 갭, 단일 종단 사례를 다시 시뮬레이션하면 결과가 그림 14에 표시됩니다. 이 얇은 유전체 층은 디커플링을 위한 일반적인 두께인 2mil로 설정됩니다. 전력면에 내장된 커패시턴스 코어. 그림 5에 표시된 것처럼 H1의 두께 1.2mm와 전원 평면 L2의 두께 1mm를 추가하면 갭 아래의 전체 유전체 두께는 8.2mm입니다.
왼쪽 이미지에서는 대부분의 복귀 전류가 기준 평면 L2의 간격 주위로 전환되는 것을 볼 수 있습니다. 오른쪽 이미지에서는 신호가 갭을 통과할 때 대부분의 복귀 전류가 전송선 아래 기준면 L3을 향해 흐르지만 일부 전류는 여전히 L2의 갭 근처에 남아 있어 약간의 노이즈를 방출합니다.
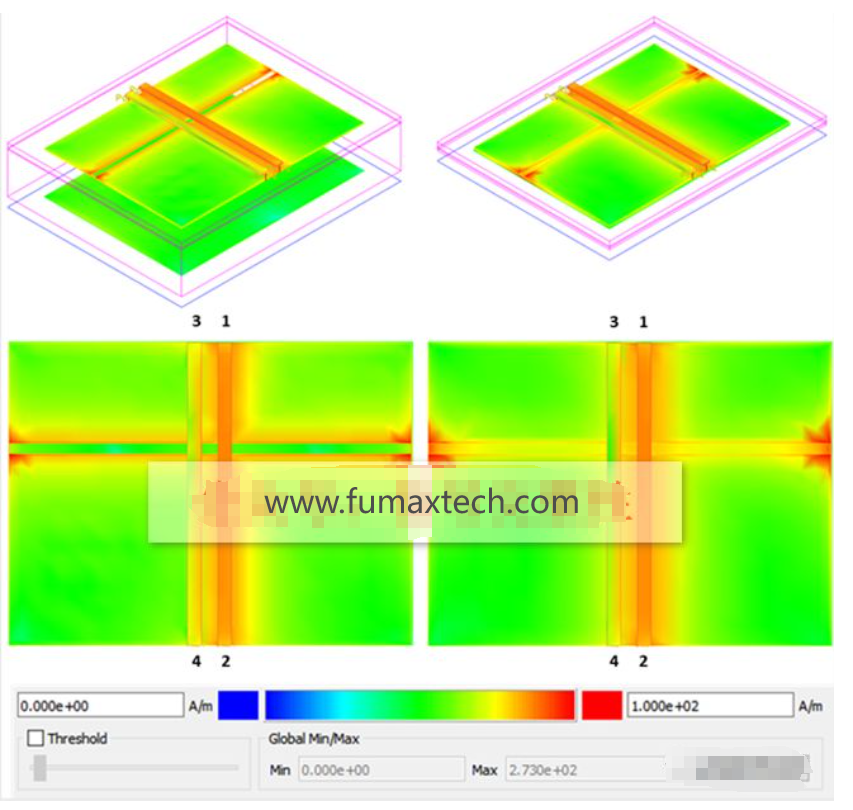
신호 무결성의 관점에서 볼 때, 그림 15에 표시된 것처럼 반사된 신호와 근단 누화 잡음은 본질적으로 절반으로 줄었습니다. 전송된 신호의 상승 시간에 대한 감쇠가 적고 원단 누화도 개선되었습니다. .
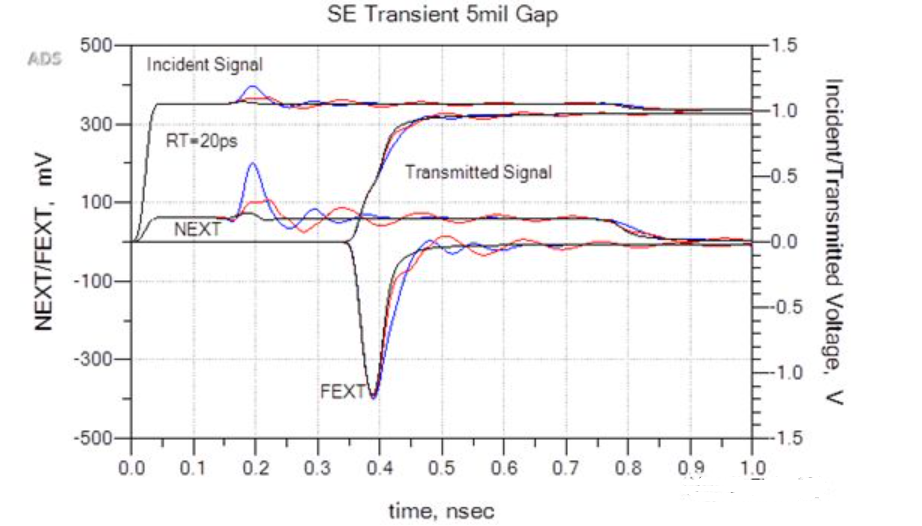
주요 질문으로 돌아가서 어떤 관점이 올바른가요? 둘 다 완전히 정확하지 않습니다. 이 기사에서는 분할 평면을 통과하는 마이크로스트립 라인의 여러 시나리오에 대해 설명합니다. 신호 무결성 관점에서 특정 조건에서는 마이크로스트립 라인이 분할 평면을 통과하는 것이 허용될 수 있습니다. 예를 들어 위의 시뮬레이션에서 분할면 사이의 간격을 5mil로 줄이고 인접한 평면층 사이에 얇은 유전체층을 추가하는 한 누화는 크게 증가하지 않습니다. 실제 소음 허용 범위에 따르면 이는 영향을 미치지 않을 수 있습니다.
하지만 EMC 입장에서는 여전히 위험과 우려가 더 큽니다. 일부 반환 전류가 분할 평면 간격의 가장자리로 절대 흐르지 않는 시나리오는 없으므로 여전히 EMI 위험이 있습니다. 실제 설계에는 상호 연관된 요소가 많기 때문에 여기나 다른 상황에 적용할 수 있는 보편적인 규칙을 갖는 것은 어렵습니다.
일반적으로 마이크로스트립 라인은 분할 평면을 교차하지 않아야 합니다. 그러나 실제 레이아웃 및 보드 스택업에 대한 자세한 분석이 가능하지 않은 경우 외부 차폐를 추가하는 등 소음 방사를 완화하는 대체 방법을 모색할 수 있습니다.
궁극적으로 이 기사에서는 최신 고속 설계에서는 신호 무결성, 전력 무결성 또는 EMC만 개별적으로 고려하는 것으로 제한할 수 없다는 점을 강조합니다. 세 가지 모두를 동시에 고려해야 합니다. EMC를 고려하지 않고 신호 무결성만 고려한다면 잘못된 결론을 도출할 수 있으며 최종 제품의 EMC 호환성 테스트가 실패할 가능성이 있습니다.