4.3.9 设计多层板时,应注意插件封装中与印刷电路板接触的金属外壳元件。顶层焊盘不得打开。它们必须涂上绿油或丝印油墨(例如两针晶体、三针LED)。
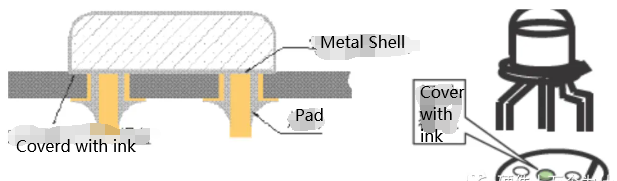
4.3.10 设计和布线PCB时,尽量减少印制板上的槽和孔,以免影响其强度。
4.3.11 贵重元件:不要将贵重元件放置在角落、边缘、安装孔、槽、面板切割边缘或拐角处。这些位置是印制板的高应力区域,很容易造成焊点和元件的裂纹和断裂。
4.3.12 较重的元件(如变压器)不应远离定位孔,以免影响印制板的强度和变形。布局时,较重的元件应放置在 PCB 下方(也是最后经过波峰焊接的一侧)。
4.3.13 变压器、继电器等发射能量的器件应远离放大器、单片机、晶振、复位电路等易受干扰的器件和电路,以免影响工作的可靠性。
4.3.14 对于 QFP 封装的 IC(需要波峰焊工艺),必须以 45 度角放置,并包含焊盘(如图所示)。
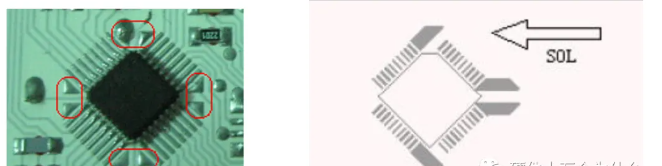
4.3.15 表面贴装元件波峰焊时,在插入元件(如散热片、变压器等)的周围和下方不应开散热孔,以防止第一波峰(干扰波峰)的焊锡与上板上的元件或元件引脚粘连,在后续工序组装时产生异物。
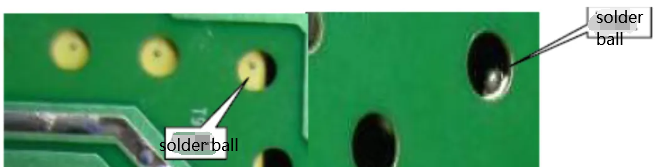
4.3.16 大面积铜箔需用绝缘胶带与焊盘连接。
为了保证良好的焊锡渗透性,大面积铜箔上的元件焊盘必须用绝缘胶带连接到焊盘上。对于需要5A以上电流的焊盘,不能使用绝缘焊盘。 (见图)

4.3.17 为避免回流焊后器件错位和立碑,应保证0805及以下表贴器件两端散热对称性。焊盘和印刷导体之间的连接宽度不应超过0.3mm(对于非对称焊盘),如上图所示。
4.4 元件库选型要求
4.4.1 应确认现有PCB元件封装库的选择正确。
PCB上现有元件库中元件的选择应保证封装与元件的物理形状、引脚间距、孔径等相匹配。
对于通孔元件,元件引脚与通孔之间的公差应配合良好(通孔直径大于引脚直径的8-20mil),公差可适当加大,以保证良好的配合。焊料渗透。无特殊要求时,手插元件过孔规格如下:
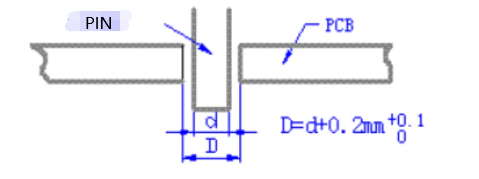
4.4.2 元件直径应系列化,5mil以上增加40mil,即40mil、45mil、50mil、55mil,4mil以下减少40mil,即36mil、32mil 、28 万、24 万、20 万、16 万、12 万、8 万。
4.4.3 器件引脚直径与PCB焊盘孔径、插头引脚焊盘孔径与回流焊对应关系如下:
装置引脚直径 (D) | PCB焊盘孔径/THT回流焊焊盘孔径) |
直径≤1.0mm | 直径+0.3mm/+0.15mm |
1.0毫米 | 直径+0.4mm/0.2mm |
直径>2.0毫米 | 直径+0.5mm/0.2mm |
建立元件封装库时,孔径的单位应转换为英制单位(mil),且孔径应满足系列化要求。
4.4.4焊盘形状设计:
4.4.4.1 元件焊盘的设计原则上应符合以下几点:
4.4.4.1.1 尽量使垫的方向与水流方向垂直。
4.4.4.1.2 焊盘的宽度最好等于或略大于元件的宽度;垫的长度略小于垫的宽度。
4.4.4.1.3 增大元件焊盘之间的间隙有利于装配;建议使用小垫子。
4.4.4.1.4 MT元件焊盘上或焊盘附近不应有通孔;否则,回流焊接时,焊盘上的焊料会沿着通孔流动,造成虚焊、焊锡不足,甚至可能流到板的另一面造成短路。
4.4.4.1.5 焊盘两端走线应均匀或具有相似的热容量。
4.4.4.1.6 焊盘尺寸必须对称。
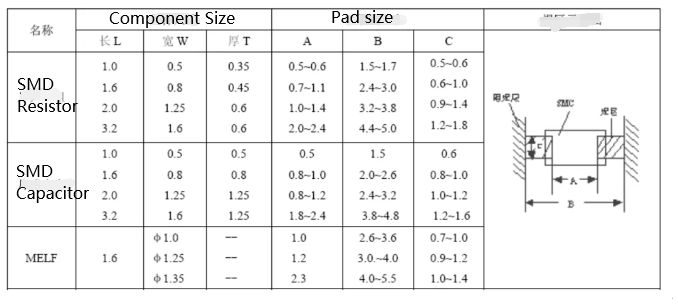
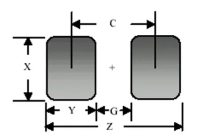
4.4.4.2 片式元件焊盘形状设计(见上图): 片式元件焊盘的典型设计尺寸如下表所示。每个焊盘外部可设计相应的阻焊膜。阻焊膜的作用是防止焊接过程中出现焊桥。
无源元件焊盘设计尺寸——电阻、电容、电感(见下表,也可参考上图和表格)
Part | Z(毫米) | G(毫米) | X(毫米) | Y(参考) | |
片式电阻器和电容器 | 0201 | 0.76 | 0.24 | 0.30 | 0.26 |
0402 | 1.45 ~ 1.5 | 0.35 ~ 0.4 | 0.55 | 0.55 | |
C0603 | 2.32 | 0.72 | 0.8 | 1.8 | |
R0603 | 2.4 | 0.6 | 1.0 | 0.9 | |
L0603 | 2.32 | 0.72 | 0.8 | 0.8 | |
C0805 | 2.85 | 0.75 | 1.4 | 1.05 | |
R0805 | 3.1 | 0.9 | 1.6 | 1.1 | |
L0805 | 3.25 | 0.75 | 1.5 | 1.25 | |
1206 | 4.4 | 1.2 | 1.8 | 1.6 | |
1210 | 4.4 | 1.2 | 2.7 | 1.6 | |
1812 | 5.8 | 2.0 | 3.4 | 1.9 | |
1825 | 5.8 | 2.0 | 6.8 | 1.9 | |
2010 | 6.2 | 2.6 | 2.7 | 1.8 | |
2512 | 7.4 | 3.8 | 3.2 | 1.8 | |
3216(A型) | 4.8 | 0.8 | 1.2 | 2.0 | |
钽电容器 | 3528(B型) | 5.0 | 1.0 | 2.2 | 2.0 |
6032(C型) | 7.6 | 2.4 | 2.2 | 2.6 | |
7343(D型) | 9.0 | 3.8 | 2.4 | 2.6 | |
2012(0805) | 3.2 | 0.6 | 1.6 | 1.3 | |
3216(1206) | 4.4 | 1.2 | 2.0 | 1.6 | |
3516(1406) | 4.8 | 2.0 | 1.8 | 1.4 | |
5923(2309) | 7.2 | 4.2 | 2.6 | 1.5 | |
2012芯片(0805) | 3.0 | 1.0 | 1.0 | 1.0 | |
电感器 | 3216芯片(1206) | 4.2 | 1.8 | 1.6 | 1.2 |
4516芯片(1806) | 5.8 | 2.6 | 1.0 | 1.6 | |
2825Prec(1110) | 3.8 | 1.0 | 2.4 | 1.4 | |
3225Prec(1210) | 4.6 | 1.0 | 2.0 | 1.8 | |
无源元件焊盘设计尺寸:
元件 | 长度(mm) | 宽度(mm) |
---|---|---|
电阻 | 0.9 - 1.3 | 0.4 - 0.7 |
电容器 | 0.9 - 1.3 | 0.4 - 0.7 |
电感 | 0.9 - 1.3 | 0.4 - 0.7 |
具体设计尺寸及配置请参考上图及表格。
4.4.4.3 SOP、QFP 焊盘设计:SOP、QFP 焊盘尺寸可根据IPC-SM-782 进行设计。
对于SOP、QFP焊盘的设计标准(如下表):
焊盘的尺寸应根据元件的尺寸来确定。焊盘宽度=引脚宽度+2*引脚高度以获得最佳焊接效果。焊盘长度如图 L2 所示,(L2 = L + b1 + b2;b1 = b2 = 0.3mm + h;h = 元件引脚高度)
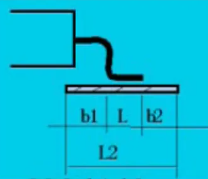
4.4.4.4 当无特殊要求时,通孔安装元件焊盘的规格如下:
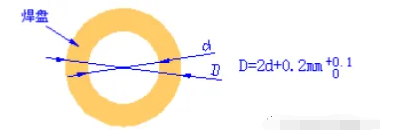
4.4.4.5 对于手插PIN、电容等,引脚间距≤2.0mm,焊盘规格为: ① 多层板焊盘直径=孔径+0.2~0.4mm; ② 单层板焊盘直径=2×孔径
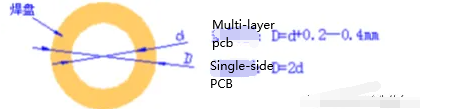
4.4.4.6 常见表面贴装IC焊盘设计,见附件(下图只是选型,具体尺寸见附件)
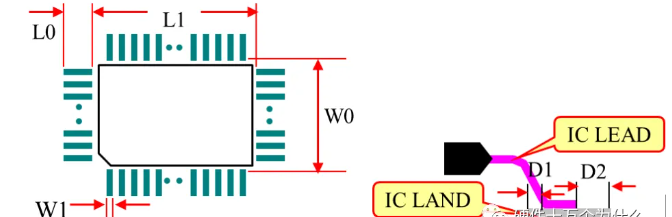
4.4.5 应正确建立新器件PCB元件封装库
4.4.5.1 PCB上没有现有元件封装库的器件应根据器件数据建立新的元件封装库,并保证丝印库存与实物相符,特别是新建立的电磁元件、自制结构元件等是否符合要求。 ,将元件库与数据(确认函、规格表、图纸)相匹配。新器件应建立能满足不同工艺要求(回流焊、波峰焊、通孔回流焊)的元件库。
4.4.5.2 需要波峰焊的SMT元件应使用表面贴装波峰焊焊盘库。
4.4.5.3 应尽量减少轴向元件和跳针的种类,以减少元件的成型和安装工具。
4.4.5.4 不同PIN间距兼容器件应有单独的焊盘孔,特别是与封装继电器兼容的焊盘应连接。
4.4.5.5 表面贴装元件不宜作为手工焊接的调试元件,因为表面贴装元件在手工焊接时很容易因热冲击而损坏。
4.4.5.6 除非实验验证没有问题,否则不应选择热膨胀系数与PCB显着不同的表面贴装元件,因为这可能导致焊盘分层。
4.4.5.7 除非实验验证没有问题,否则非表面贴装元件不应用作表面贴装元件。这可能需要手动焊接,这将导致效率和可靠性低下。
4.4.5.8 对于多层PCB,作为焊脚的一侧局部镀铜必须保证每层都有铜箔连接,以增加镀铜层的附着强度。同时,一定要进行实验验证,没有问题。否则,双面板不能使用侧面镀铜作为焊脚。
4.4.6 需要波峰焊的单面背板元件的安全距离,为防止波峰焊时的阴影效应,SMT元件之间的距离应满足以下要求:
- 同类型元件之间的距离(如图所示)
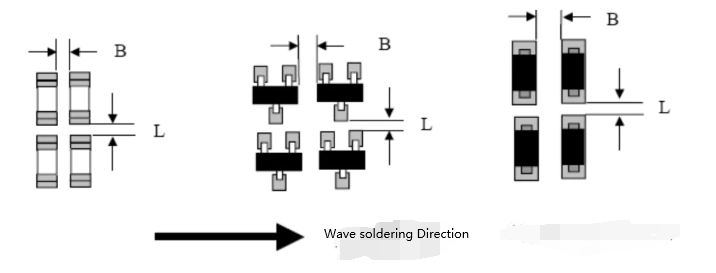
4.6.1 同一类型的SMD元件间距应≥0.3mm,不同类型元件之间的间距应≥0.13*h+0.3mm(注:h指两个不同零件之间的最大高度差) 、THT元件间距应便于操作和更换。
4.6.2贴装元件焊盘外侧与相邻贴装元件外侧的距离应大于2mm。
4.6.3 经常插拔的元件或板边连接器周围3mm范围内应避免贴片元件,以防止连接器插拔时对元件造成应力损坏。
4.6.4 定位孔中心到表面贴装元件边缘的距离应不小于5.0mm。
4.6.5 大于0805封装的陶瓷电容应放置在靠近传输边缘或应力较小的区域,其轴向应与板的入口方向平行,大于1825的陶瓷电容应尽可能避免使用可能的。 (保留意见)
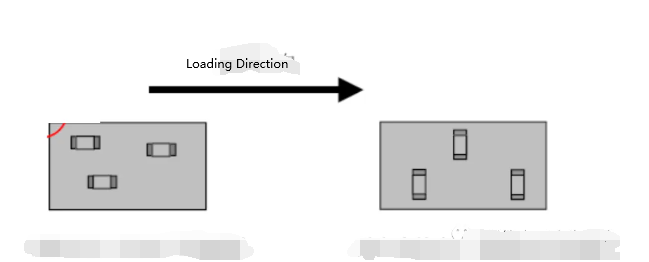
4.4.6.6 经常插拔的元件或板边连接器周围3mm范围内应避免使用SMD,以防止连接器插拔时对元件造成应力损坏。见图:
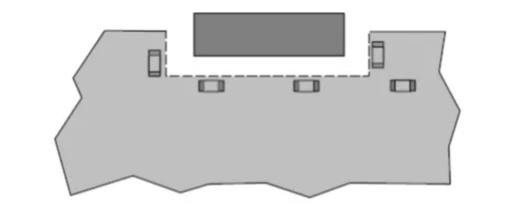
4.4.6.7 用于波峰焊的表面贴装元件应满足规定的支座要求。波峰焊表面贴装元件的间距应小于0.15mm。否则,不应将它们放置在 B 面进行波峰焊。如果元件的间距在0.15mm到0.2mm之间,可以在元件本体下方放置铜箔,以减少元件底部与PCB表面之间的距离。
4.4.6.8 确定波峰焊时通孔焊点的最小安全距离,以保证波峰焊时焊点不桥接,背面测试点边缘之间的距离应大于1.0mm。
4.4.6.9 需要波峰焊接的通孔元件焊盘间距应大于1.0mm,以保证波峰焊接时焊点不桥接(包括元件引脚焊盘边缘之间的间距)。通孔元件引脚的优选间距(节距)≥2.0mm
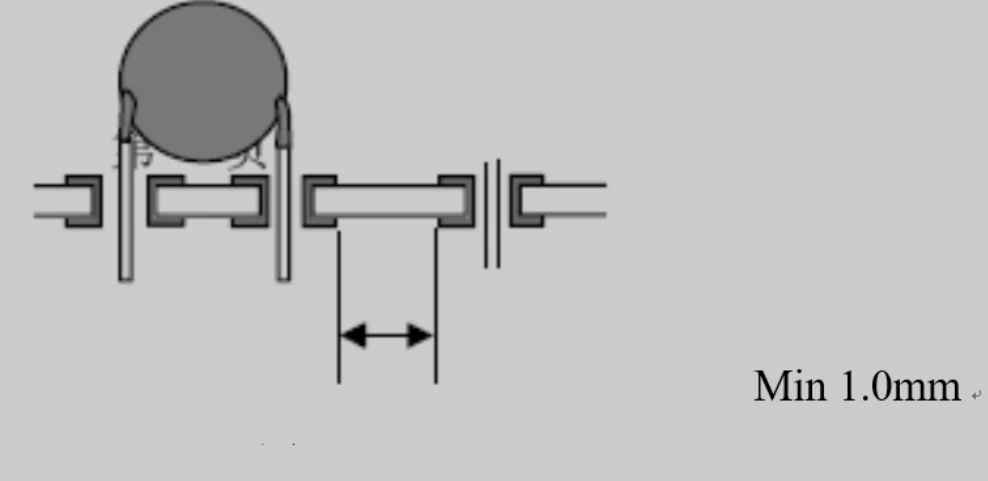
4.4.6.10 当插件元件每排引脚较多,且元件排列时焊盘与 PCB 插入方向平行时,相邻焊盘边缘间距在 0.6-1.0mm 之间的推荐做法是采用椭圆形形状焊盘或添加镀锡焊盘。
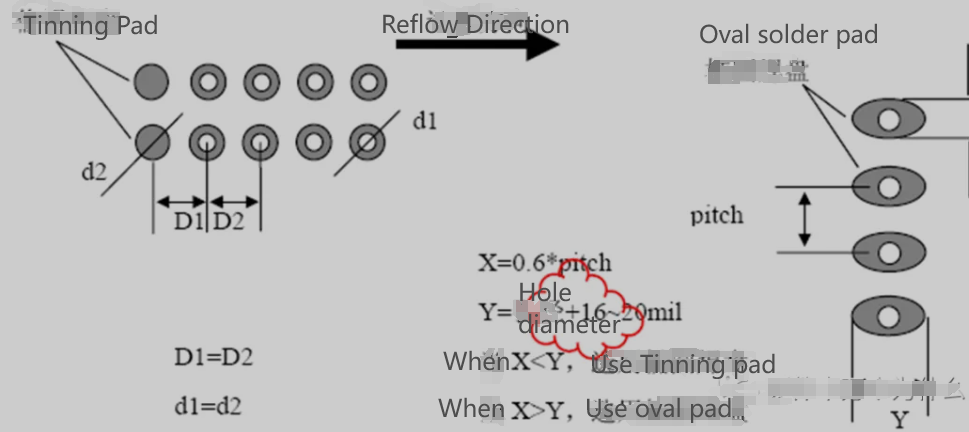
4.4.6.11 表面贴装元件之间的最小间距应满足下列要求:
对于机器放置:
- 同类型元件之间:≥0.3mm
- 不同类型元件之间:≥0.13*h+0.3mm(其中h为相邻元件之间的最大高度差)
对于手动放置:
- 元件之间:≥1.5mm。
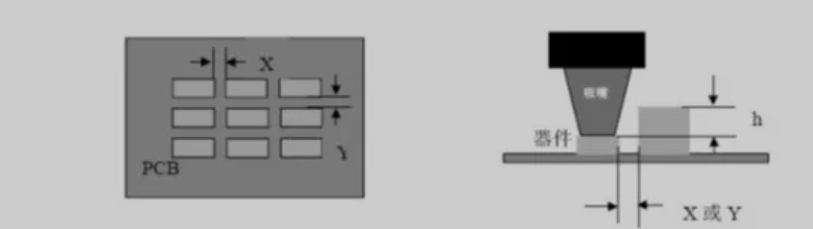
4.4.6.12 元件外边缘到板走线边缘的距离应大于或等于5mm。这是为了确保传送轨道的爪子在波峰焊或回流焊期间不会接触到元件。如果不满足此要求,则应对PCB进行边缘处理,且元件与V-CUT之间的距离应≥1mm。
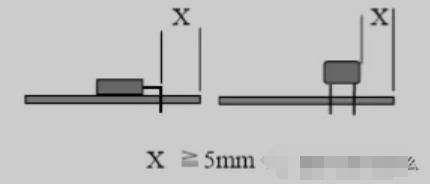
4.4.6.13 可调、可插拔部件周围应留有足够的空间,以便调试和维护。可调元件的方位和可插拔元件的预留空间应根据PCBA安装布局和可调元件的调试方法来确定。
4.4.6.14 所有插入式磁性元件必须有坚固的底座,禁止使用无底座的插入式电感。
4.4.6.15 避免极化变压器的引脚对称设计。当引脚未连接电路时,请确保添加焊盘以增加焊接强度。
4.4.6.16 安装孔的禁止区域内不得放置任何元件或走线(不包括安装孔本身的走线和铜箔)。
4.4.6.17 金属外壳部件与其他部件之间的距离应符合安全规定。金属外壳部件的布置应保证与其他部件的距离符合安全规定。
4.4.6.18 采用通孔回流焊的元件布局要求:对于非输送边缘尺寸大于300mm的PCB,应避免在PCB中间放置较重的元件,以减少焊接时插入元件的重量对PCB变形的影响,以及插入元件对元件的影响已经放在板上了。 b.为了便于插入,元件应放置在靠近插入操作的一侧。 C。对于较长的元件(如存储卡插槽),长度方向应与输送方向一致。当元件的多个引脚在同一直线上时,连接器、DIP封装元件、T220封装元件的排列应使其轴线与波峰焊方向平行。二极管、1/4W电阻等较轻的元件应排列使其轴线与波峰焊方向垂直。这可以防止波峰焊接期间由于一端先于另一端固化而导致的浮动,并避免对通孔元件使用方形焊盘(这可能导致焊接和桥接不良)。